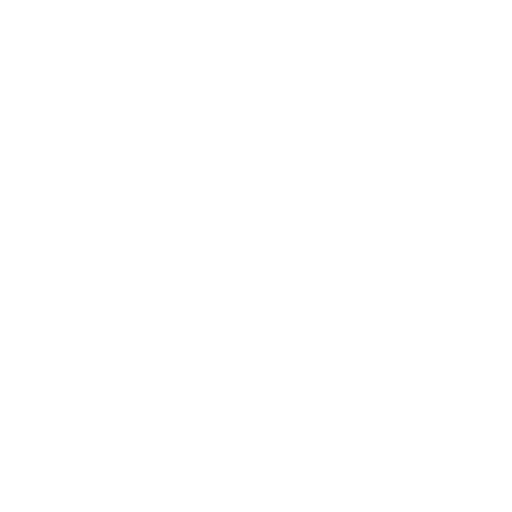

An Introduction to Cracking
Petroleum and petroleum products have a vital role in our daily life. Crude oil and natural gas are extracted from the land and transported to refineries where it undergoes several physical and chemical changes. The raw materials in the petroleum industry are known as feed stocks. In the refinery, these feed stocks undergo a process called cracking where complex organic molecules break down into lighter molecules and these have high commercial value. Hence, cracking is an essential process in such fields.
Cracking Meaning
In petrochemistry, petro geology and in Organic Chemistry, the word cracking defines the breakdown of complex long chain molecules like hydrocarbons into simple molecules by breaking their carbon-carbon bonds. It is the most important step for the commercial production of petroleum and other petroleum products. Usually, cracking is done either under high temperature and pressure conditions or under the influence of catalysts. When catalysts are used, the requirement of high temperature conditions can be minimised and hence it is a way of saving energy.
Process of Cracking
Initiation- Free radicals are important to undergo the process of Initiation. One molecule is broken into two free radicals. Out of the two, the smaller one undergoes the process of initiation.
Hydrogen Abstraction- Hydrogen is removed from the second molecule thereby making it a free radical.
Radical Decomposition- Free radicals break into other free radicals to form alkene products.
Radical Addition- Then the free radicals react with the alkenes.
Termination- Two radicals react with each other to form a non-free radical product in the process of termination.
Types of Cracking in Petrochemistry
Thermal Cracking
Thermal cracking is the breakdown of complex long-chain hydrocarbons into lighter particles by using high temperature conditions. The major products of thermal cracking are olefins. Depending on the product range, two types of thermal cracking are known. The first one is steam cracking or pyrolysis which is carried under high temperature conditions ~750 to 9000c in the absence of oxygen, which produces ethylene and other feedstocks valuable in petrochemical industries.
The second type of temperature cracking is known as delayed coking which is carried out under a relatively lower temperature range ~5000c. The product of delayed coking is a highly crystalline petroleum coke called needle coke which is used in the production of electrodes in steel and aluminium industries. Modern high pressure thermal cracking operates at 7,000 kPa.
Steam Cracking
Steam cracker units are facilities in which feedstocks such as naphtha, LPG, butane, ethane, and propane are thermally cracked by using steam in a bank of pyrolysis furnaces. Steam cracking is done in the absence of oxygen. It is the principal industrial method for producing the lighter alkenes including ethene and propene. Steam cracking is the core technology that supports the largest scale chemical processes, that is, ethylene and propylene.
Fluid Catalytic Cracking (FCC)
Through FCC high boiling point, high molecular weight crude oil is converted into gasoline olefinic acid and other petroleum products. Generally, the feedstock is a heavy gas oil having a molecular weight that ranges from 200 to 600 or higher and the boiling point is in the range of 340oC. In the FCC process, heavy gas oil feedstock is heated to a high temperature and to a moderate pressure and then placed in a bed of hot powdered catalyst which breaks the long chain high boiling point hydrocarbon liquid to short chain molecules and the vapours are collected.
The commonly used catalysts in FCC are solid acid catalysts like silica-alumina and zeolite. The catalytic cracking proceeds at a relatively lower temperature which saves energy. Since it operates at a lower temperature, the amount of alkene produced is minimum. Alkene causes instability to hydrocarbon fuels.
HydroCracking
Hydrocracking is the breakdown of high boiling point heavy molecules into distillates and gasolines in presence of hydrogen and a catalyst. The major hydrocracking catalysts are Al2O3 /SiO2 impregnated with nickel, molybdenum, cobalt, or tungsten. The whole reaction is carried out inside a hydro cracker. There are two main reactions taking place inside a hydro cracker - catalytic breakdown of heavy hydrocarbons into lighter unsaturated hydrocarbons and the saturation of these newly formed hydrocarbons with hydrogen. The major products obtained through hydrocracking are jet fuels, diesel, kerosene, and other petroleum products. Along with this, low sulphur naphtha fractions and LPG are produced.
Cracking in Organic Chemistry
In Organic Chemistry, cracking of long chains of organic molecules takes place by free radical mechanism. The reaction is generally carried out in the presence of light. The reaction intermediate is a free radical which is highly reactive and undergoes rearrangement. The C-C bond breaks homolytically and the products are mainly alkenes and alkanes.
The major steps in cracking of organic molecules are given below.
Initiation: Here, a single molecule cleaves homolytically produce 2 free radicals.
CH3CH3 → 2 CH3
Abstraction of hydrogen: One of the formed free radical absorbs hydrogen from the other molecule and a new free radical is formed.
CH3• + CH3CH3 → CH4 + CH3CH2•
Radical decomposition: Here, free radical breaks into other free radicals and an alkene.
CH3CH2• → CH2=CH2 + H
Radical addition: In this step, free radical reacts with alkene and forms a new free radical.
CH3CH2• + CH2=CH2 → CH3CH2CH2CH2•
Termination: Here, 2 free radicals react together to form molecules.
CH3• + CH3CH2• → CH3CH2CH3
CH3CH2• + CH3CH2• → CH2=CH2 + CH3CH3
Difference Between Thermal Cracking and Catalytic Cracking
Key Features of Cracking
Cracking is a process by which complex molecules are broken into lighter molecules.
It has a vital role in the commercial production of petroleum and other petroleum products.
Thermal cracking, steam cracking, hydro cracking, and fluid catalysed cracking are the different types of cracking.
In Organic Chemistry, cracking is generally done by the homolytic fission of carbon-carbon bonds in presence of light.
Conclusion
Cracking is an important chemical process in petroleum and Organic Chemistry. Here, large molecules of hydrocarbons break and form important lighter hydrocarbons, mainly alkenes and other aromatic compounds. Depending on the temperature condition and catalysts used, different types of crackings are there and their product ranges are also different. It is an important reaction in petroleum industries which helps in the commercial production of diesel, gasoline, LPG, etc.
FAQs on Cracking
1. What is cracking in chemistry?
In chemistry, cracking is a process where complex, long-chain organic molecules, particularly hydrocarbons, are broken down into simpler, lighter molecules. This is achieved by breaking the carbon-carbon bonds, typically under conditions of high temperature and pressure, or with the use of a catalyst.
2. What are the main products obtained from cracking larger hydrocarbons?
The primary goal of cracking is to produce commercially valuable, lighter hydrocarbon fractions. Key products include:
- High-octane gasoline for vehicles.
- Lighter alkenes like ethene and propene, which are vital feedstocks for the petrochemical industry.
- Jet fuels, diesel, and kerosene.
- Liquefied Petroleum Gas (LPG).
3. What are the primary types of cracking used in the industry?
There are several methods of cracking, which can be broadly categorised based on the conditions used. The main types are:
- Thermal Cracking: Uses high temperatures (around 750-900°C) and pressure to break down molecules. A key example is steam cracking.
- Catalytic Cracking: Employs a catalyst to facilitate the reaction at lower temperatures. Examples include Fluid Catalytic Cracking (FCC) and Hydrocracking.
4. How does the free-radical mechanism explain the process of cracking?
In organic chemistry, cracking often proceeds via a free-radical mechanism. The process involves several key steps:
- Initiation: A molecule breaks homolytically (due to heat or light) to form two highly reactive free radicals.
- Hydrogen Abstraction: A free radical removes a hydrogen atom from another hydrocarbon molecule, creating a new free radical.
- Radical Decomposition: The new free radical breaks down into a stable alkene molecule and a smaller free radical.
- Termination: The reaction stops when two free radicals combine to form a stable, non-radical product.
5. What is the fundamental difference between thermal cracking and catalytic cracking?
The fundamental difference lies in the method used to break the hydrocarbon chains. Thermal cracking relies solely on very high temperatures and pressures. In contrast, catalytic cracking uses a catalyst (like zeolites or silica-alumina) which allows the process to occur at relatively lower temperatures and pressures. This not only saves energy but also produces a higher yield of gasoline with less unstable alkenes.
6. Why is cracking so important for the petroleum refining industry?
Cracking is a cornerstone of the modern petroleum industry because it adds immense commercial value. Crude oil naturally contains a large proportion of heavy, long-chain hydrocarbons (like heavy gas oil) with low demand. Cracking converts these low-value fractions into high-demand, high-value products like gasoline, jet fuel, and LPG, effectively matching the output of a refinery to market needs.
7. How is cracking different from fractional distillation?
Although both processes are vital in oil refining, they are fundamentally different. Fractional distillation is a physical separation process that separates crude oil into different fractions based on their boiling points, without changing their chemical structure. In contrast, cracking is a chemical decomposition process that breaks the chemical bonds within large hydrocarbon molecules to create smaller, different molecules.
8. What determines the ideal feedstock for cracking?
The ideal feedstock for cracking consists of high-boiling point, high-molecular-weight hydrocarbon fractions that have lower commercial value in their raw state. Examples include heavy gas oil, naphtha, and other long-chain alkanes. These are chosen because their conversion into lighter products like gasoline and alkenes represents the most significant increase in economic value.
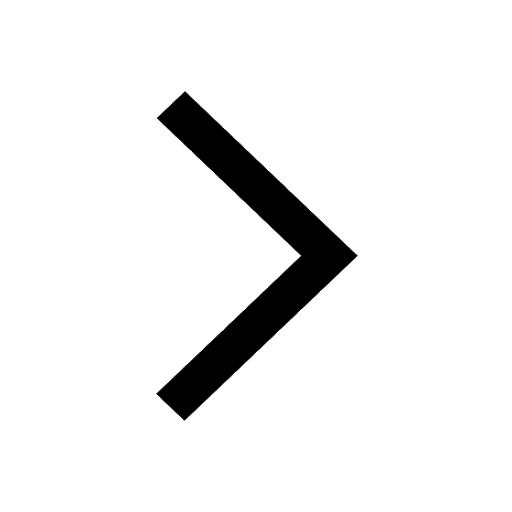
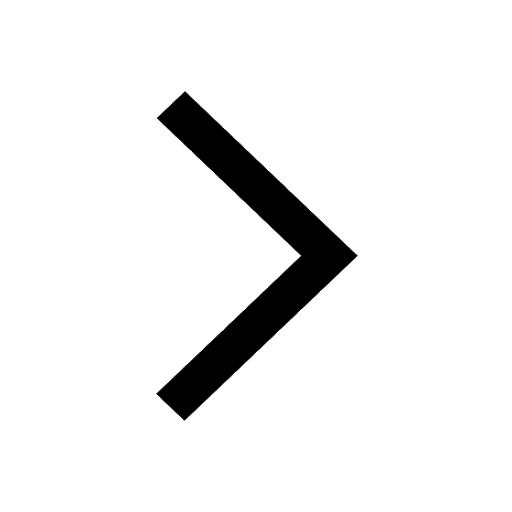
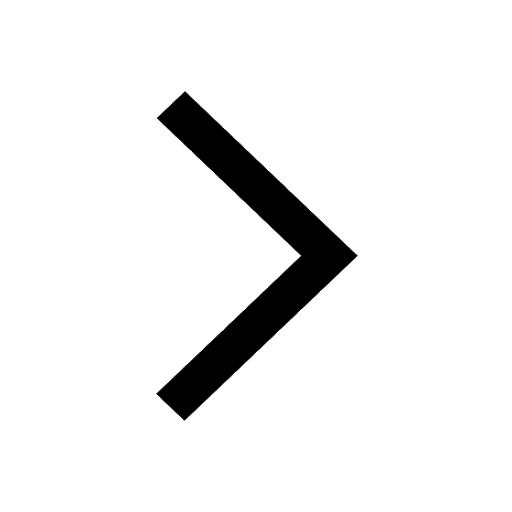
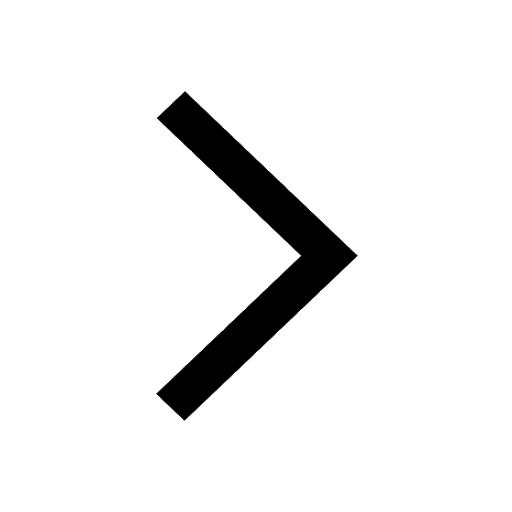
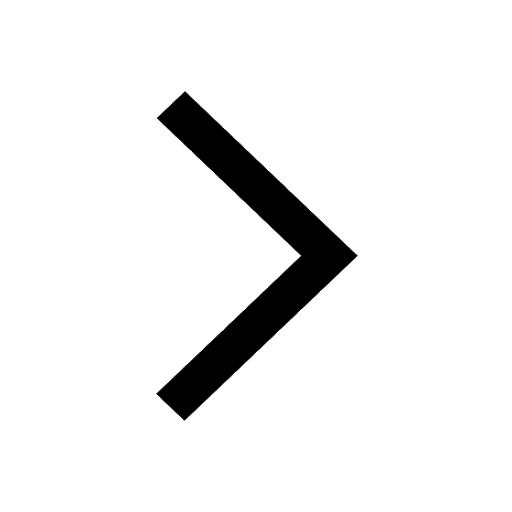
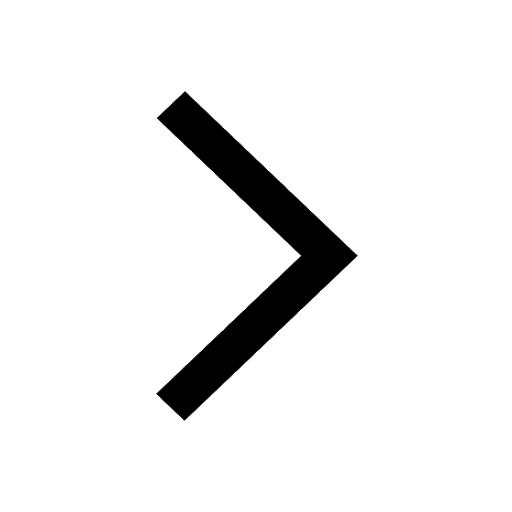
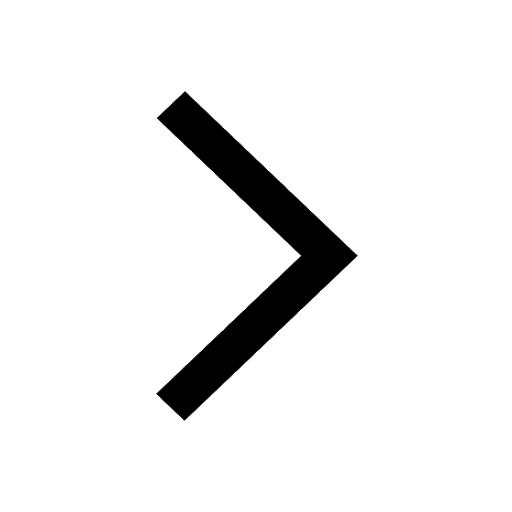
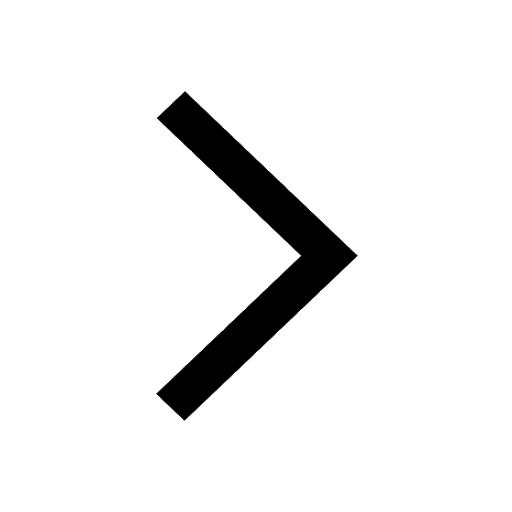
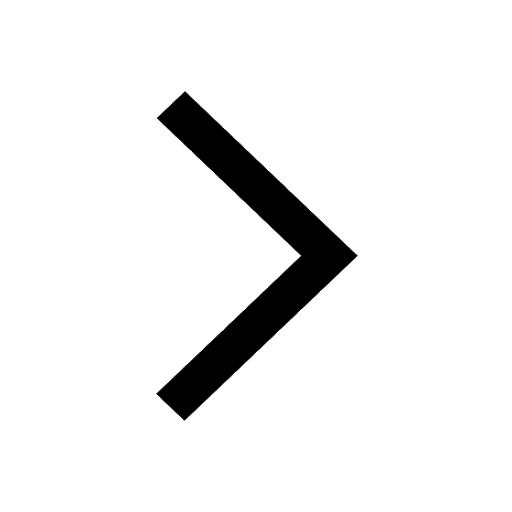
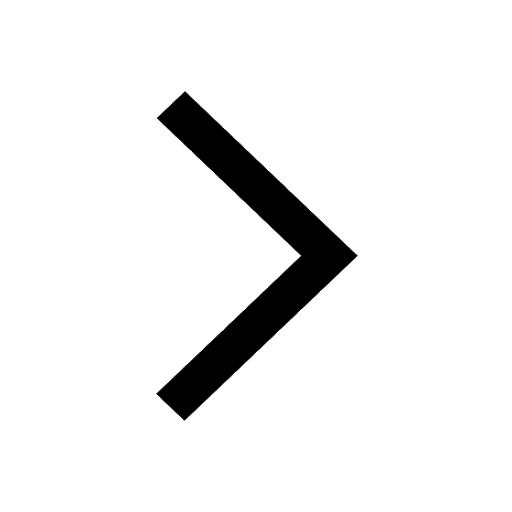
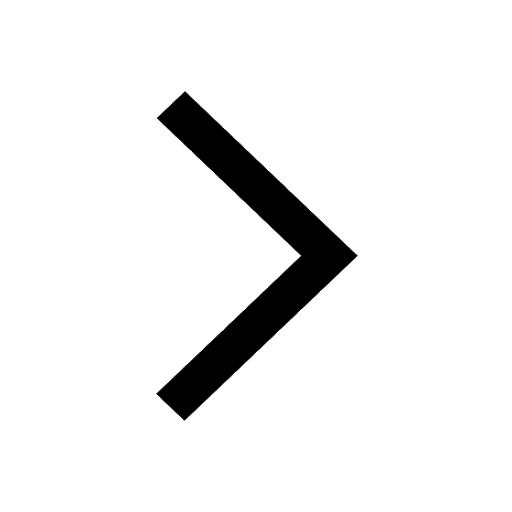
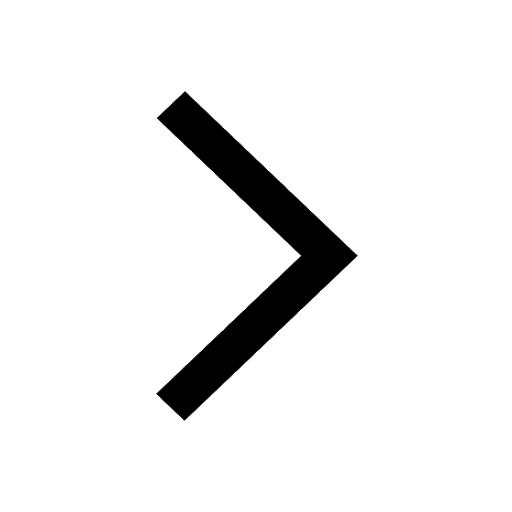
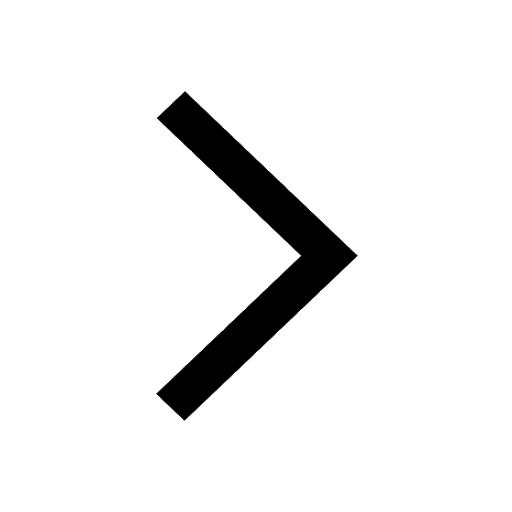
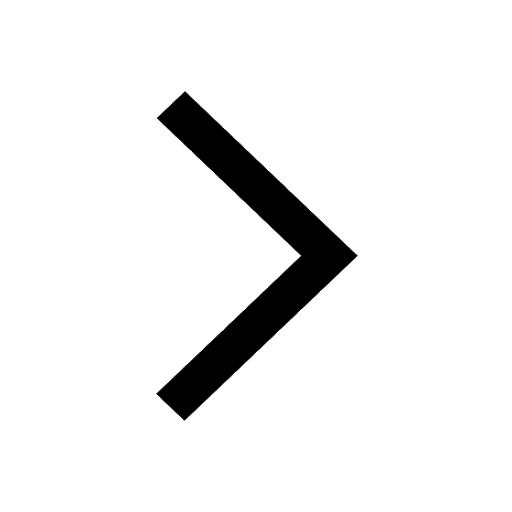
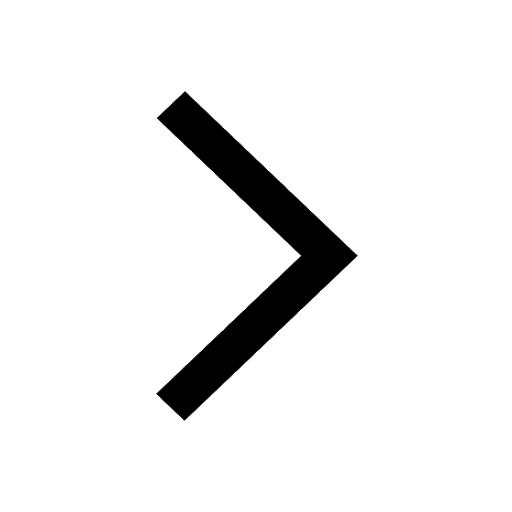
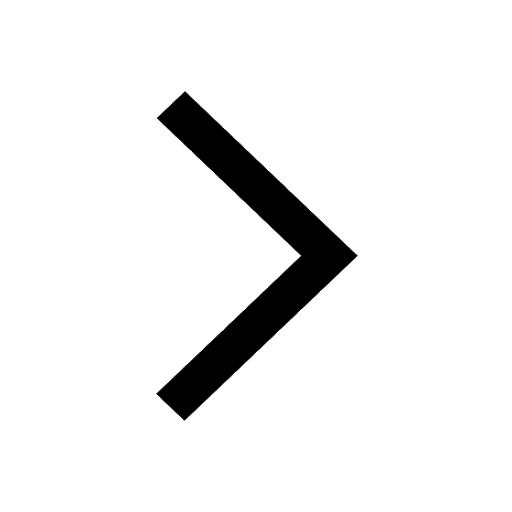
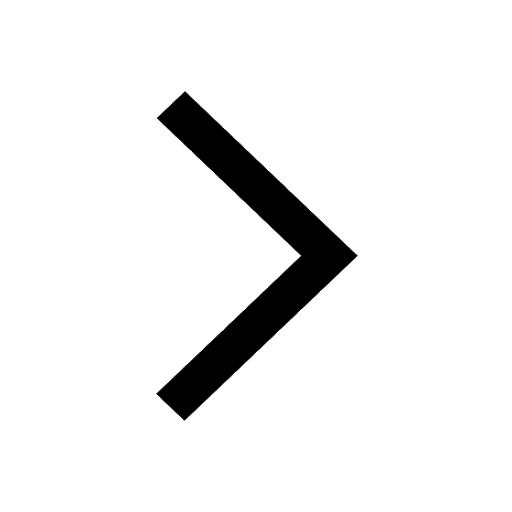
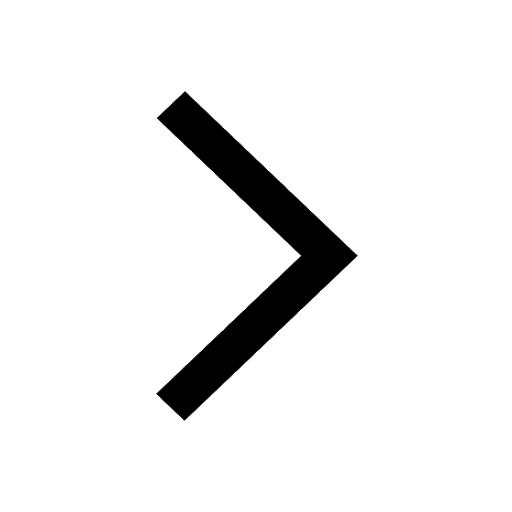