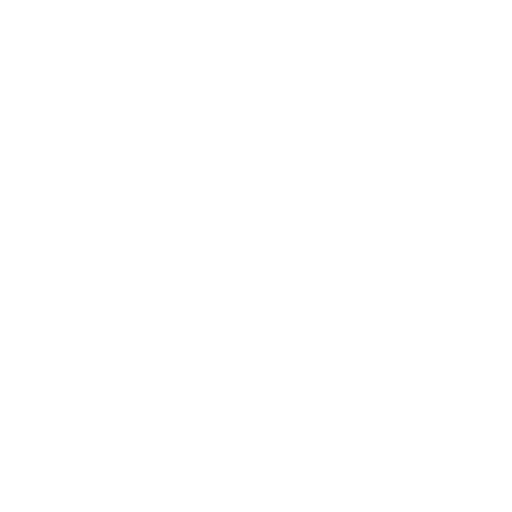

What is Polytetrafluoroethylene?
Polytetrafluoroethylene (PTFE) is a tough, solid, nonflammable and waxy synthetic resin formed by tetrafluoroethylene polymerization. It is known by such trademarks as Fluon, Teflon, Polyflon, and Hostaflon, PTFE material is distinguished by its high melting point, resistance, and slippery surface to attack by almost all the chemicals. These properties have made it more familiar to the consumers as the coating on nonstick cookware; it is fabricated into industrial products, including pipeliners, bearings, and parts for pumps and valves.
About Polytetrafluoroethylene
PTFE material was first discovered serendipitously by Roy Plunkett in 1938, an American chemist for E.I. du Pont de Nemours & Company (now - DuPont Company), who found that a gaseous tetrafluoroethylene refrigerant tank had been polymerized to a white powder. It was also applied as a corrosion-resistant coating during World War-II to protect the metal equipment that can be used in the handling of radioactive material for the Manhattan Project. Due to the difficulty faced in devising methods for handling the high-melting, slippery stuff, PTFE saw no industrial use for more than a decade after the war. DuPont then, in 1960, released its trademarked Teflon-coated nonstick cookware.
Tetrafluoroethylene (C2F4) is an odourless and colourless gas, which is made by heating chlorodifluoromethane (CHClF2) at a temperature range of 600–700 °C. Chlorodifluoromethane, in turn, can be obtained by reacting the hydrogen fluoride (H.F.) with chloroform (CHCl3). Tetrafluoroethylene monomers (which are small, single-unit molecules) are either emulsified or suspended in water and then polymerized (that are linked into giant multiple-unit molecules) under high pressure in the free-radical initiator presence. The polymer contains a chain of carbon atoms having two fluorine atoms that are bonded to each carbon:
The fluorine atoms that surround the carbon chain, such as a protective sheath, create a relatively dense and chemically inert molecule with very strong bonds of carbon-fluorine. The polymer can be inert to most chemicals, which does not melt at less than 327 °C, and contains the lowest coefficient of friction of any well-known solid. These properties enable the usage of bearings and bushings that require no lubricant, as the liners for equipment. They can be used in the transportation and storage of organic solvents and strong acids, as the electrical insulation under the conditions of high-temperature, and in its most familiar application, as a cooking surface, which does not need oil or fat uses.
PTFE product’s Fabrication is not easy due to the material not flowing readily even above its melting point. At the same time, the moulded parts are made by heating and compressing fine powders mixed with volatile lubricants. To provide a permanent coating, metallic surfaces are dipped or coated with an aqueous dispersion of PTFE particles. PTFE dispersions are also woven into fibres.
Production
PTFE material can be produced by free-radical polymerization of tetrafluoroethylene. The net equation is given as follows:
n F2C=CF2 → −(F2C−CF2)n−
Since tetrafluoroethylene may explosively decompose into carbon and tetrafluoromethane, special polymerization apparatus might be needed to avoid hot spots that could induce this dangerous side reaction. Typically, this process is initiated with persulfate, which hemolyzed in generating sulfate radicals:
[O3SO−OSO3]2− ⇌ 2 SO4−
The resulting polymer can be terminated with the ester groups of sulfate, which can be hydrolyzed to form O.H. end-groups.
Since PTFE is poorly soluble in almost every solvent, the polymerization is conducted as in water emulsion. Also, this process produces a suspension of polymer particles. In an alternate way, the polymerization can be conducted using a surfactant like PFOS.
Applications
The primary application of PTFE, consuming up to 50% of production, is for the insulation of wiring in computer applications (for example, coaxial cables, hookup wire) and aerospace. This particular application exploits the fact that PTFE has outstanding dielectric properties, especially at higher radio frequencies, by making it suitable for use as an excellent insulator in cables and connector assemblies and in the printed circuit boards, which are used at microwave frequencies. This makes the choice of material, combined with its high melting temperatures, as a high-performance substitute for the weaker and lower-melting-point polyethylene, commonly used in low-cost applications.
In industrial applications, due to its low friction, PTFE is used for plain bearings, gears, slide plates, gears, gaskets, seals, bushings and other sliding parts applications where nylon and acetal outperform.
Safety
PTFE Pyrolysis can be detectable at 200 °C, and it evolves many fluorocarbon gases and a sublimate. An animal study was conducted in 1955, and it concluded that it is unlikely that these products would be produced at temperatures below 250 °C in quantities affecting health. Products such as nonstick coated cookware have had their PFOA removed since 2013, and before this, products that contain PFOA were not found to be the major sources of exposure.
Ecotoxicity
Sodium trifluoroacetate, including the similar compound chlorodifluoroacetate, can both be generated when PTFE undergoes thermolysis process and produces longer chain polyfluoro- and/or poly chloroform- (C3-C14) carboxylic acids as well, which can be equally persistent. A few of these products have recently been linked with possible adverse environmental and health impacts and are being phased out of the U.S. market.
FAQs on Polytetrafluoroethylene
1. What is Polytetrafluoroethylene (PTFE)?
Polytetrafluoroethylene, commonly known as PTFE, is a synthetic fluoropolymer of tetrafluoroethylene. It is a tough, nonflammable, and waxy solid known for its exceptional chemical resistance, high melting point, and extremely low coefficient of friction, making it very slippery. It is widely recognised by brand names like Teflon.
2. What is the monomer unit and basic structure of Polytetrafluoroethylene?
The monomer unit of Polytetrafluoroethylene is tetrafluoroethylene (C₂F₄). During polymerization, these monomer units link together to form a long chain polymer. The repeating unit in the polymer chain is represented by the formula −(F₂C−CF₂)n−, which consists of a carbon atom backbone completely sheathed by fluorine atoms.
3. What are the key properties of PTFE that make it so useful?
PTFE's usefulness stems from its unique combination of properties. Key properties include:
- Chemical Inertness: It is resistant to attack by almost all chemicals and solvents.
- High Thermal Stability: It maintains its properties over a wide range of temperatures, with a high melting point of approximately 327°C.
- Low Coefficient of Friction: It has one of the lowest friction coefficients of any known solid, making it ideal for non-stick surfaces and lubricants.
- Excellent Electrical Insulation: It has outstanding dielectric properties, making it a superb insulator for wiring and electronics.
4. How is Polytetrafluoroethylene manufactured?
PTFE is produced through the free-radical polymerization of its monomer, tetrafluoroethylene (C₂F₄). This process is typically conducted as an emulsion or suspension in water under high pressure, using a free-radical initiator like persulfate. The equation for the polymerization is: n F₂C=CF₂ → −(F₂C−CF₂)n−. Special equipment is required to manage the reaction safely, as tetrafluoroethylene can decompose explosively.
5. Is Teflon the same as Polytetrafluoroethylene?
Yes, Teflon is a well-known trademark for Polytetrafluoroethylene (PTFE). While PTFE is the chemical name of the polymer, Teflon is the brand name under which DuPont first marketed it, particularly for non-stick cookware. Other trademarks for PTFE also exist, such as Fluon and Polyflon.
6. Why is PTFE so chemically resistant and slippery?
The exceptional properties of PTFE are a direct result of its molecular structure. The polymer consists of a long chain of carbon atoms completely surrounded by fluorine atoms. The carbon-fluorine (C-F) bonds are extremely strong and stable. This protective sheath of fluorine atoms shields the carbon backbone from chemical attack, making the molecule chemically inert. It also results in weak intermolecular forces, which contributes to its very low coefficient of friction or 'slipperiness'.
7. What are some common applications of PTFE beyond non-stick pans?
While famous for cookware, PTFE has many critical industrial and niche applications. These include:
- Aerospace and Electronics: Used as high-performance insulation for wiring and coaxial cables due to its excellent dielectric properties.
- Industrial Parts: Fabricated into gaskets, seals, bearings, and liners for pipes and pumps that handle corrosive chemicals.
- Medical Applications: Used for creating grafts and medical implants due to its inertness within the body.
- Fabric Protection: Applied to fabrics and textiles, such as school uniforms and outdoor apparel, to make them stain-resistant and waterproof.
8. Is PTFE food safe and are there any health concerns?
PTFE itself is considered a stable, non-toxic, and safe material for use in cookware at normal cooking temperatures (below 260°C or 500°F). The main health concerns were historically linked to a chemical called PFOA (perfluorooctanoic acid), which was used in the manufacturing process of PTFE. However, PFOA has been phased out of cookware production since 2013. Overheating PTFE above 350°C can cause it to decompose and release fumes that can cause flu-like symptoms, but this is well above typical cooking temperatures.
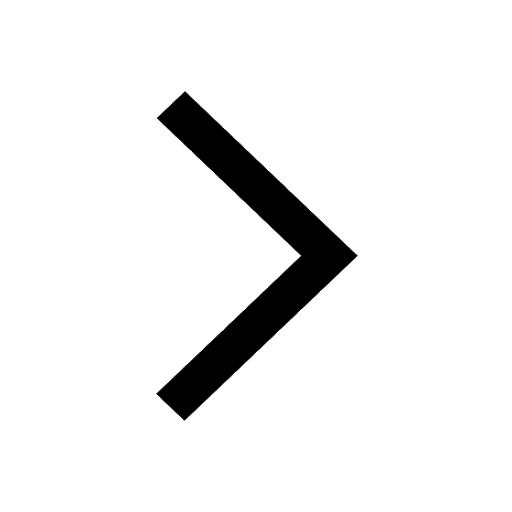
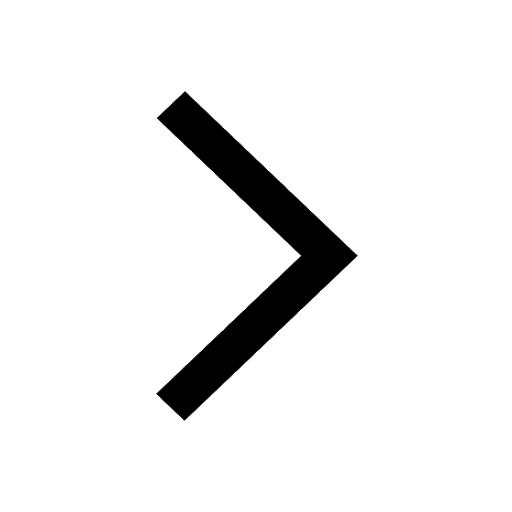
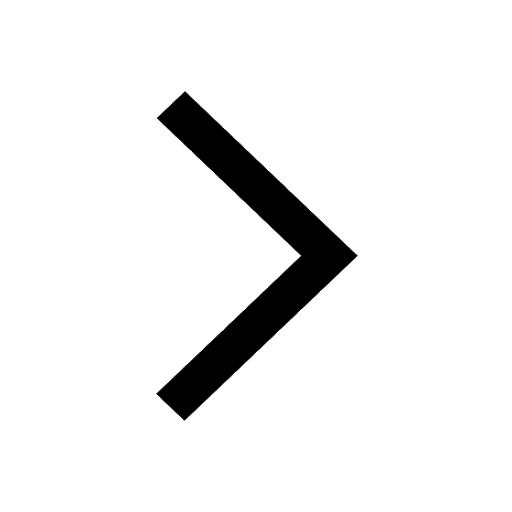
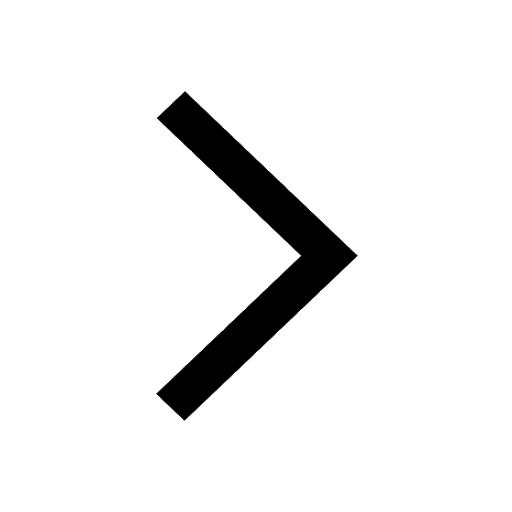
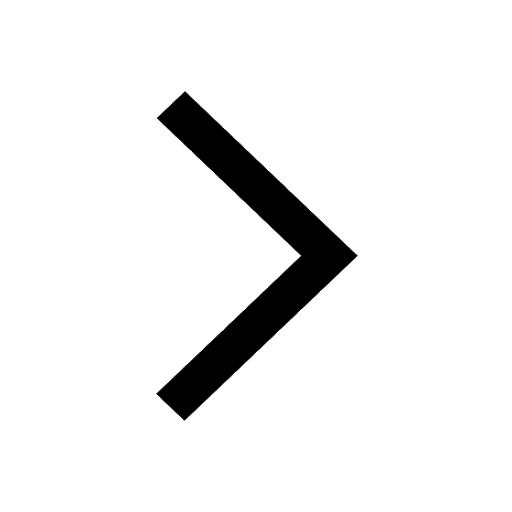
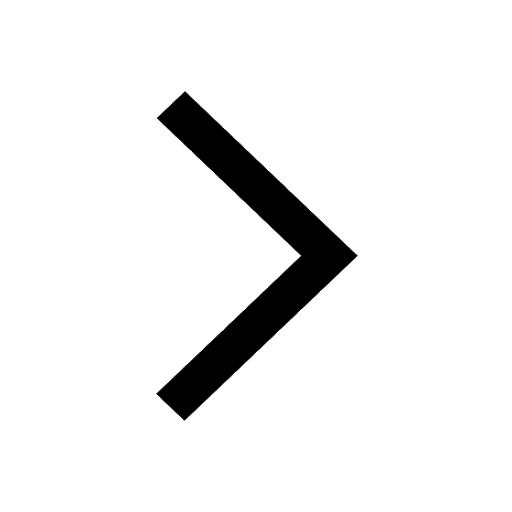
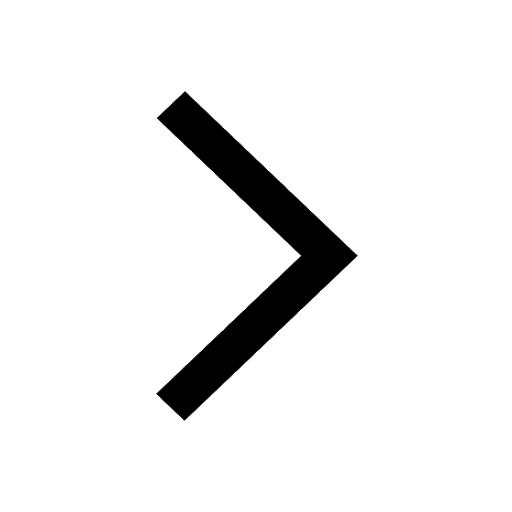
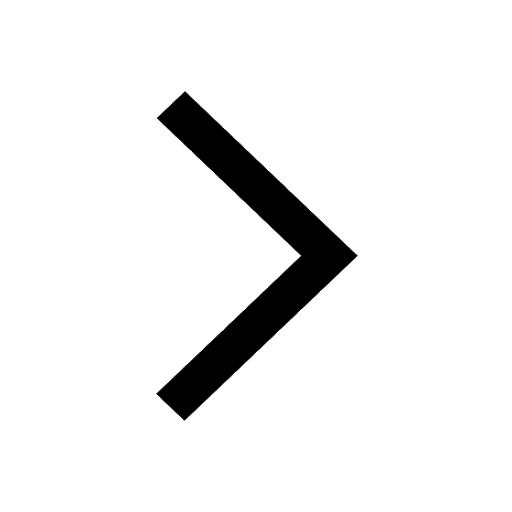
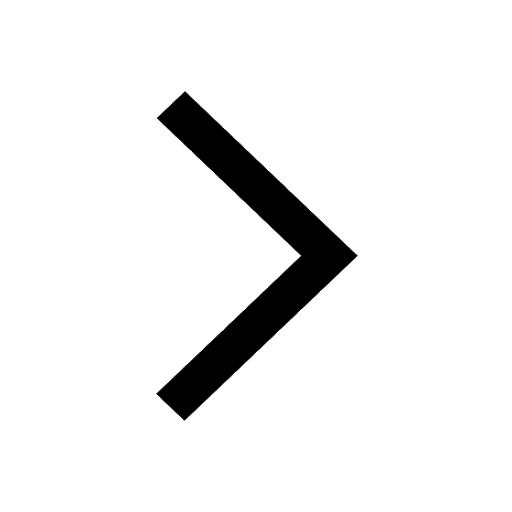
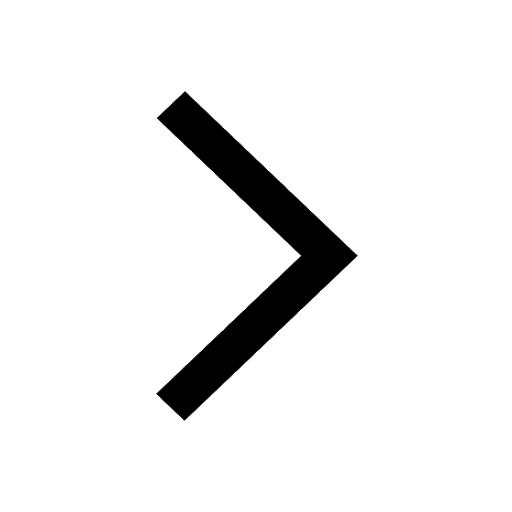
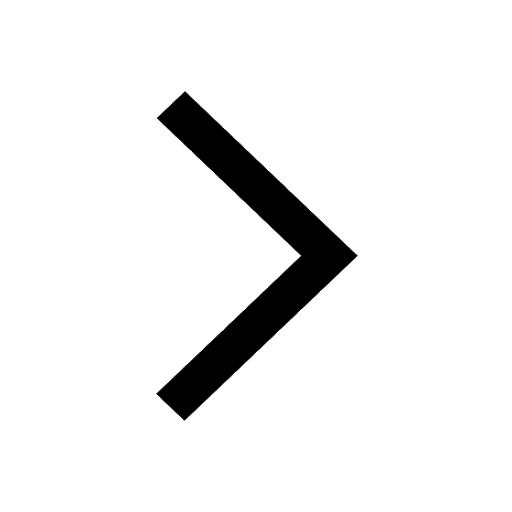
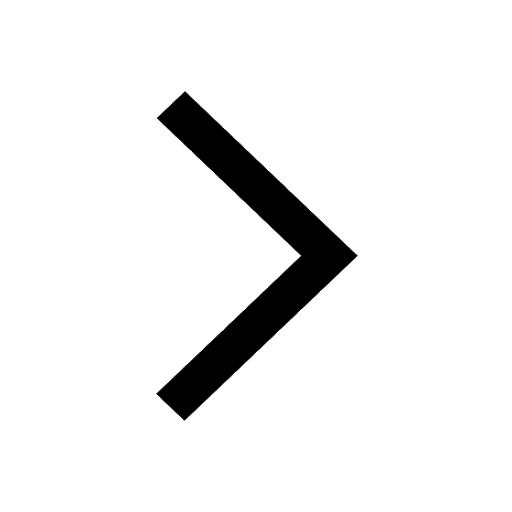
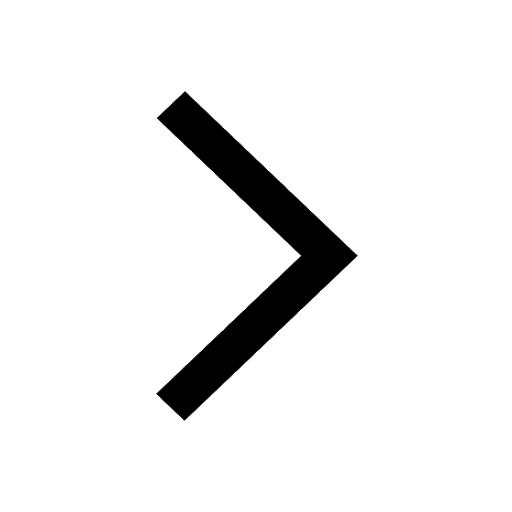
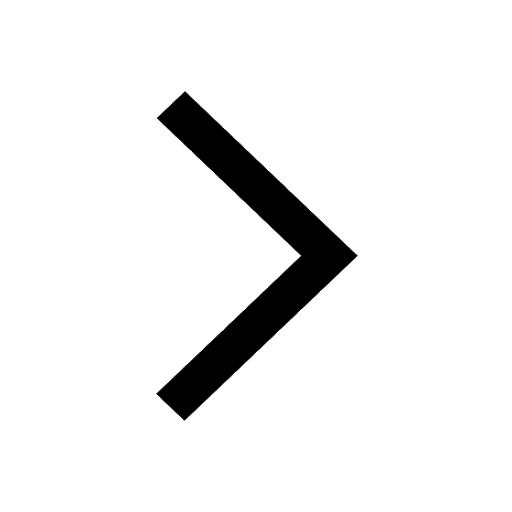
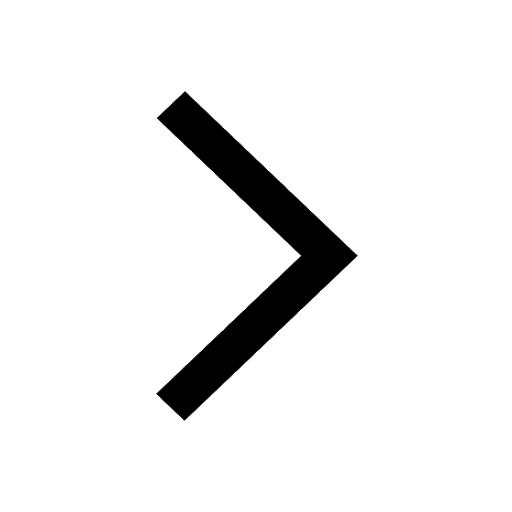
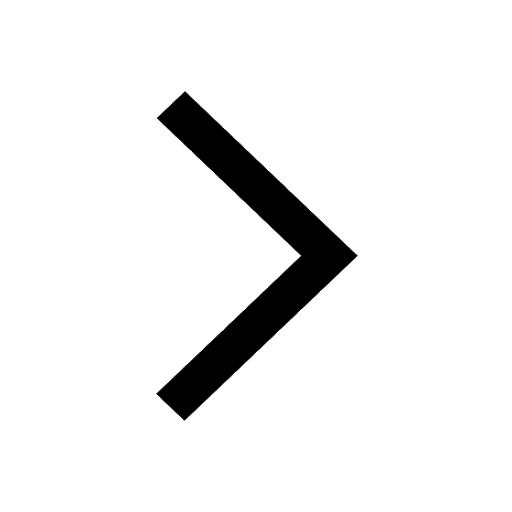
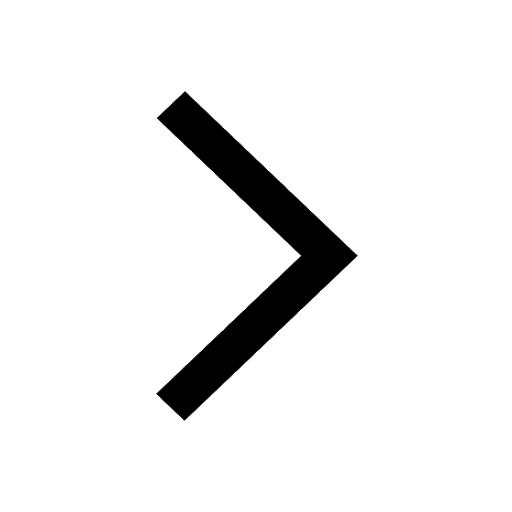
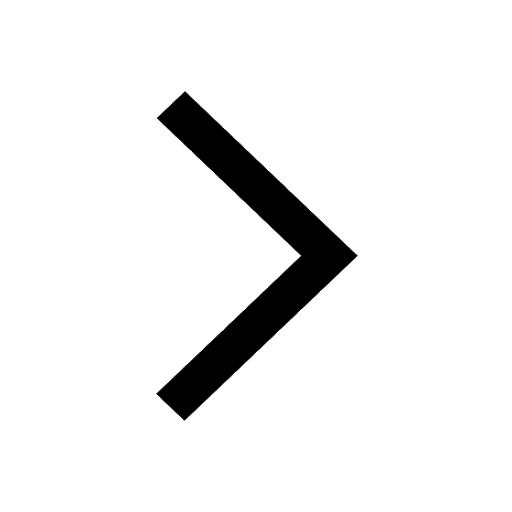