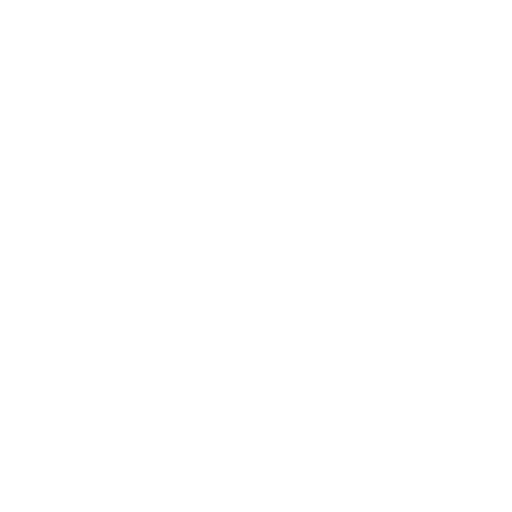

What are Thermosetting Polymers?
Thermosetting Polymers are the type of polymers where the macromolecular chains tend to bond with one another forming the cross-linked 3D network. These polymers are also known as Thermosetting plastics or Thermosets. The definition of the word Thermosetting translates to a term which means setting permanently upon heating. Thus the Thermosetting Polymers get the hard texture after they are exposed to heating to their pre-Thermoset form.
Preparation of the Thermosetting Polymers
The Thermosets or the Thermosetting Polymers are prepared using chemical reactions of a minimum of two materials. One of these reactants is the monomer that is responsible for forming the final chain of the polymer. The 2nd component is the cross-linker, also called comonomer, which acts as the substance of cross-linking. The cross-linker helps in combining two or more strands related to monomers together.
The Thermosets are generally moulded to provide them with a useful shape before they assume the hard form. The different ways in which the moulding is done includes Reaction Injection moulding (RIM), Resin transfer moulding (RTM), Extrusion moulding, Compression moulding, and Spin casting.
Properties Associated with Thermosetting Polymers
The Thermosetting Polymers tend to have a cross-linked 3D structure. The chemical and physical properties of polymers are dependent on components behind the creation of polymers. Some of the fundamental properties of the Thermosetting Polymers are as follows.
Thermosetting plastics tend to be heat resistant. However, when high intensity of heat is applied, they tend to decompose before they reach the melting point.
The Thermosetting Polymers are brittle in nature owing to loss of elasticity when they are heated.
Once cured or moulded, these polymers cannot be re-shaped through application of heat.
The Thermoset density is dependent on the constituent components that are used for creating the polymer.
Thermosets are usually resistant to chemical attacks.
The Uses of Thermosetting Polymers
Due to Thermosets having unique properties, they are highly useful for some of the daily requirements. The uses of the Thermosetting Polymers are as follows.
They are used for manufacturing permanent parts in a wide array of industries.
Thermosets are used for producing electrical goods as well as components such as panels and insulators.
Thermosets are used for manufacturing construction equipment panels.
Since they tend to be heat resistant, Thermosets are used for manufacturing heat shields.
In automobiles, Thermosets are utilised for producing brake pistons.
Thermosets are also used for various agricultural equipments that includes motors and feeding troughs.
The Examples of Thermosetting Polymers
The various examples of Thermosetting Polymers include Bakelite, Epoxy Resin, Melamine Resin, Duroplast, and Urea-Formaldehyde. These different Thermosetting Polymers are used in a variety of applications across a wide range of industries.
FAQs on Thermosetting Polymers or Thermosets
1. What are thermosetting polymers, and how are they formed?
Thermosetting polymers, also known as thermosets, are polymers that become permanently hard and rigid when heated. During their formation, low molecular mass, semi-fluid substances are heated, which initiates an irreversible chemical reaction. This reaction creates extensive covalent cross-links between the polymer chains, forming a rigid, three-dimensional network structure. Once cured, they cannot be softened or remelted, and applying excessive heat will cause them to decompose rather than melt.
2. How do thermosetting polymers differ from thermoplastics in terms of structure and properties?
Thermosetting polymers and thermoplastics differ primarily in their molecular structure and response to heat. Key differences include:
- Structure: Thermosetting polymers have a 3D cross-linked network formed by strong covalent bonds. Thermoplastics consist of long, linear or slightly branched polymer chains held together by weaker intermolecular forces.
- Effect of Heat: Thermosets undergo an irreversible chemical change upon heating and cannot be reshaped. Thermoplastics soften on heating and harden on cooling, a fully reversible process that allows them to be remoulded multiple times.
- Mechanical Properties: Thermosets are generally harder, stronger, and more brittle, while thermoplastics are typically more flexible and have higher impact strength.
- Recyclability: Due to their irreversible bonds, thermosets are not recyclable, whereas most thermoplastics are.
3. What are some common examples of thermosetting polymers and their specific applications?
Several thermosetting polymers are used extensively in various industries due to their unique properties. Common examples include:
- Bakelite (Phenol-formaldehyde resin): Used for making electrical switches, plugs, and handles for cookware due to its excellent electrical insulation and heat resistance.
- Epoxy Resins: Widely used as high-strength adhesives, protective coatings, and in the electronics industry for encapsulating circuits.
- Melamine-formaldehyde resin: Known for its hardness and durability, it is used to manufacture unbreakable crockery and decorative laminates.
- Urea-formaldehyde resin: Commonly used as an adhesive for plywood and particleboard, and for making moulded plastic items.
4. Why can't thermosetting polymers be remelted or reshaped after curing?
The inability of thermosetting polymers to be remelted or reshaped is a direct result of their molecular structure. During the initial heating, or curing process, strong and permanent covalent bonds form between the polymer chains, creating an extensive cross-linked 3D network. These strong cross-links lock the chains in place, preventing them from sliding past one another when heat is reapplied. Unlike the weak intermolecular forces in thermoplastics that allow for movement, these covalent bonds are too strong to be overcome by heat alone. Applying excessive heat will break these bonds and degrade the polymer, causing it to char or decompose instead of melting.
5. What specific properties make thermosetting polymers ideal for manufacturing electrical components and heat shields?
Thermosetting polymers are chosen for these demanding applications due to a unique combination of properties:
- For Electrical Components: Their primary advantage is high dielectric strength and exceptional electrical insulation. The rigid, cross-linked structure restricts the movement of electrons. Furthermore, their high thermal stability ensures they do not deform, melt, or lose their insulating properties under the heat generated by electrical currents, making them perfect for switches and panels.
- For Heat Shields: For these applications, their low thermal conductivity and ability to maintain structural integrity at very high temperatures are crucial. When exposed to extreme heat, thermosets undergo a process called ablation, where the surface chars to form an insulating layer that protects the material underneath.
6. What is the role of cross-linking in determining the final properties of a thermosetting polymer like Bakelite?
Cross-linking is the most critical process in defining the characteristics of a thermosetting polymer like Bakelite. The extensive network of strong covalent bonds created during cross-linking is directly responsible for transforming the initial monomers (phenol and formaldehyde) into a final product with desirable properties. This process:
- Converts the material from a fusible, low-strength substance into an infusible, rigid solid.
- Imparts exceptional mechanical strength, hardness, and durability.
- Provides high dimensional stability, meaning it resists changes in shape under load or heat.
- Is the reason for its excellent heat resistance and chemical inertness.
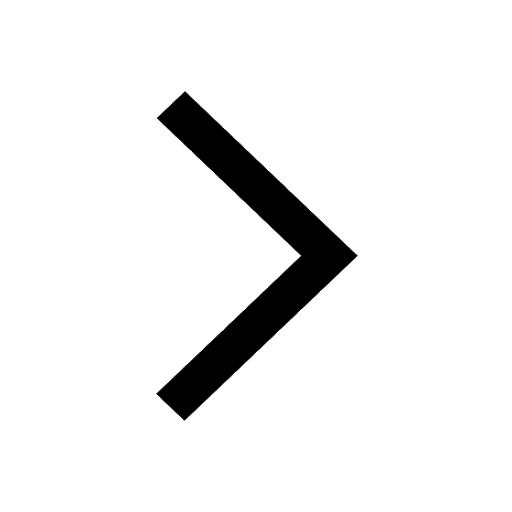
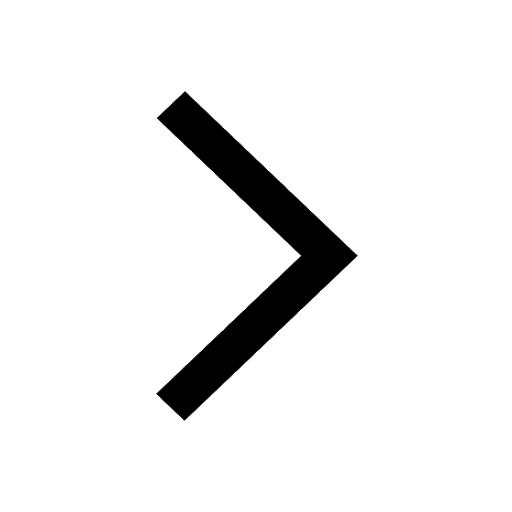
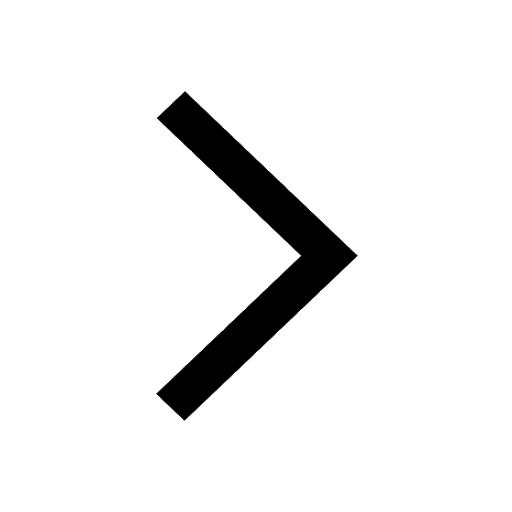
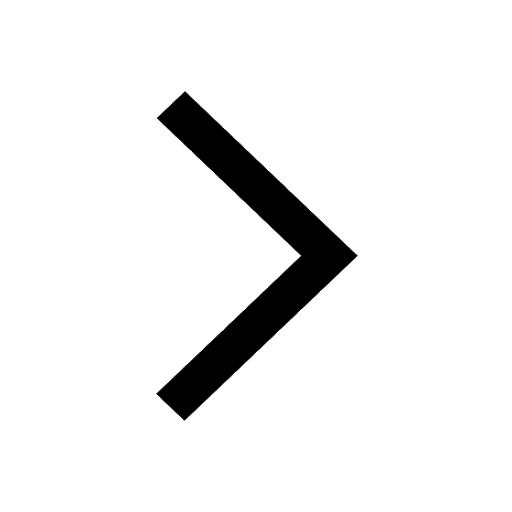
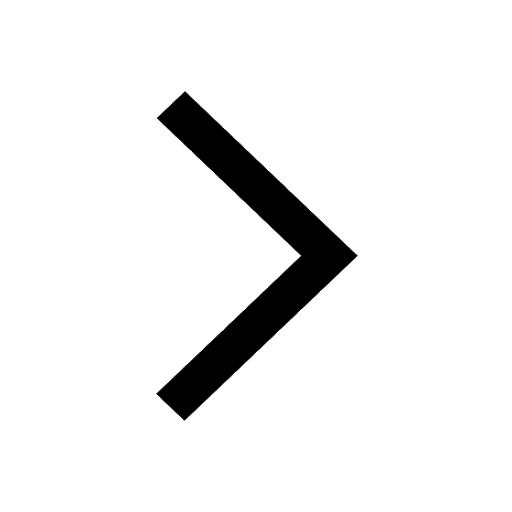
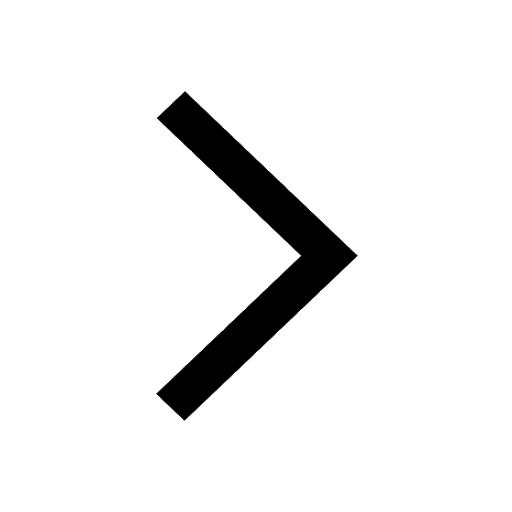
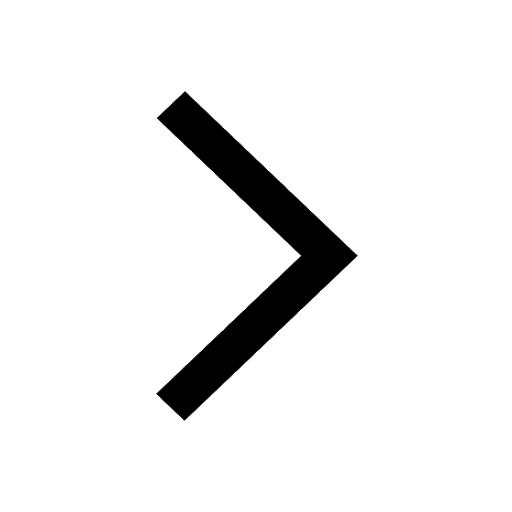
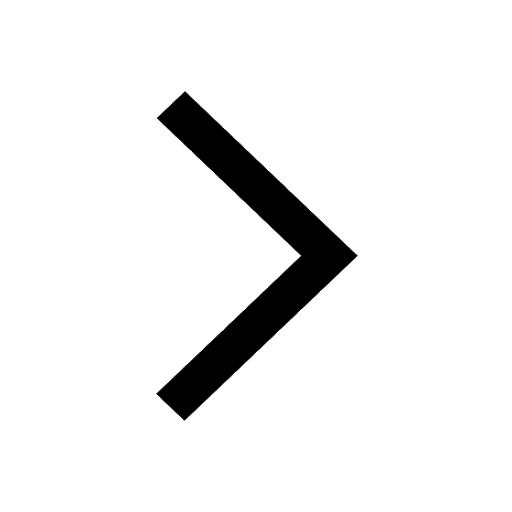
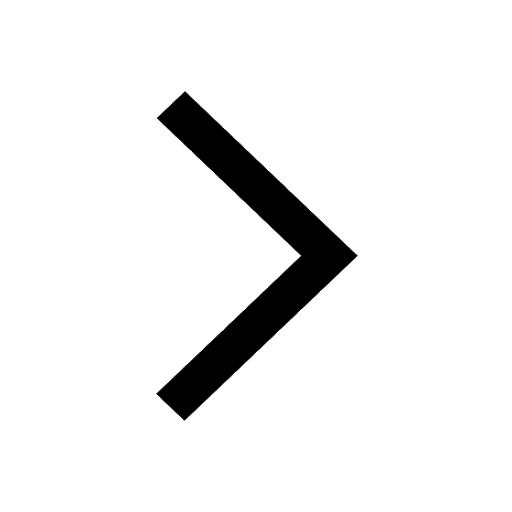
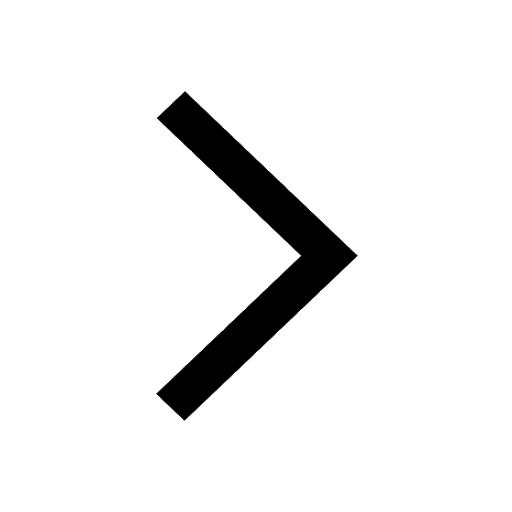
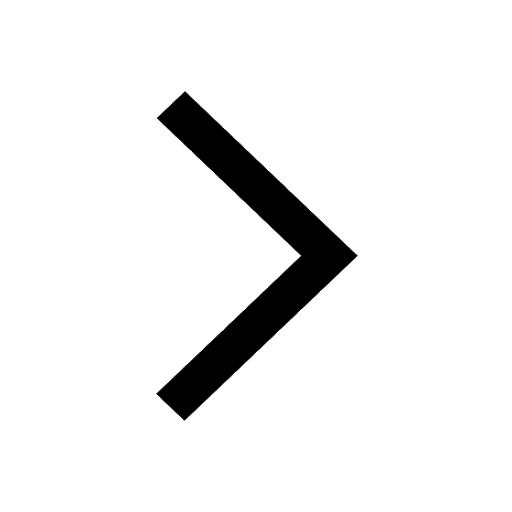
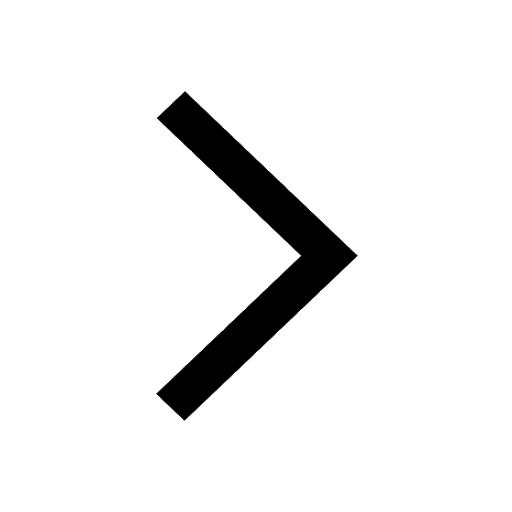
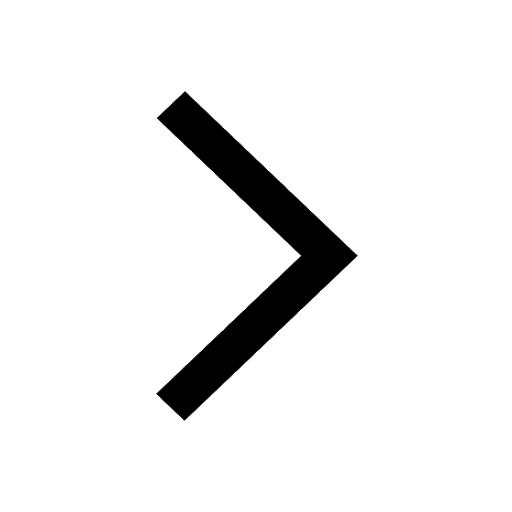
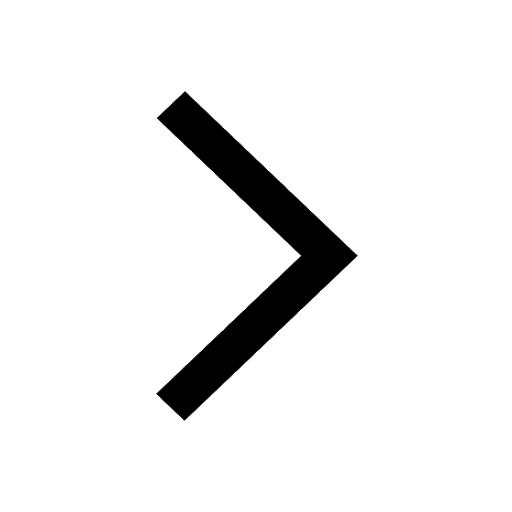
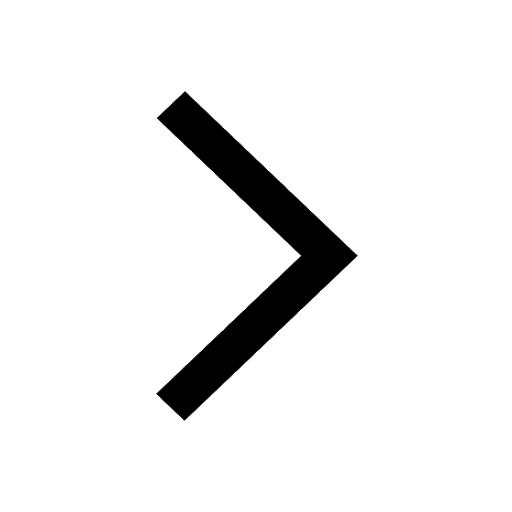
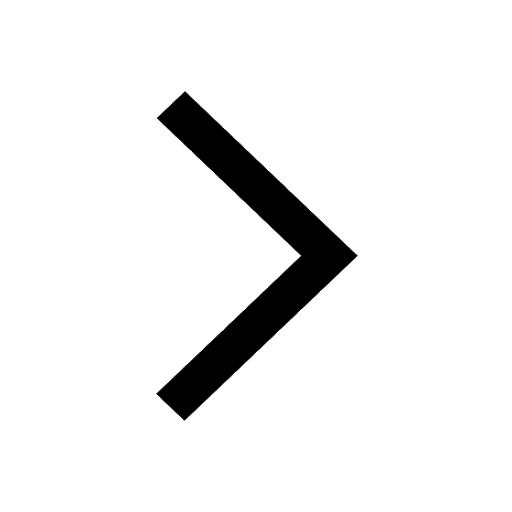
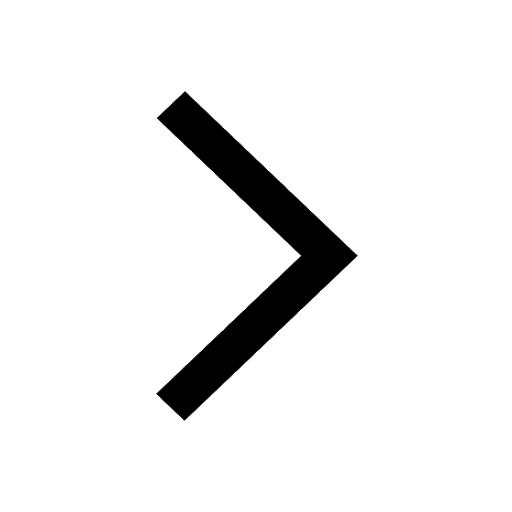
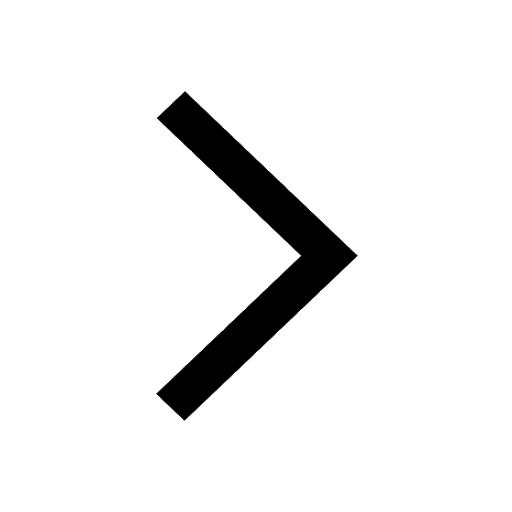