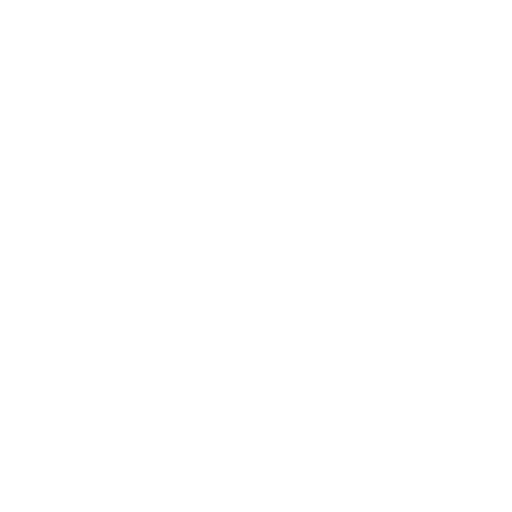

What are Techniques of Costing?
For any business, the first step before selling the products is to calculate the cost. This helps in strategically planning the production and managing the finances. To do so, the companies follow several processes depending on the needs and methods. This leads to the facilitation of making managerial decisions for cost accounting. However, before knowing the techniques of costing and types of costing methods, it is essential to understand the definition of cost accounting and its components. Let us help you understand these concepts better.
What is Cost Accounting?
Cost accounting is defined as the process of taking into account all the costs involved in the production, processing and selling of any projects or products. Under this, a complete note is taken along with the analysis of the process. Cost accounting plays a key role in helping the company make cost-effective decisions. There are several methods and techniques of costing, followed by different types of organizations.
Difference Between Cost Accounting and Financial Accounting
Oftentimes, one can get confused between cost accounting and financial accounting. However, these are two different aspects. Here are some of the key differentiators.
Traditional (financial) accounting is calculated by deducting the expenses from the total cost to calculate the profits. However, in the case of cost accounting, the complete process and production are made cost-effective by reducing the costs at every step and aspect.
In traditional accounting, the organization is viewed as a whole, whereas in cost accounting, the organization is segregated on several bases, including production and process units.
The techniques and methods of financial accounting are constant with all types of business. However, the methods and techniques of cost accounting vary depending on the types of businesses.
Elements of Cost
For any business or production unit, the costs can be majorly divided on the following basis. These include:
Material costing
Labour costing
Other expenses
The further classification for these includes:
Direct costing
Indirect costing
Standards of Cost Accounting
The uniformity and guidance for costing are provided to the business by the Cost Accounting Standards Board (CASB) constituted by the Institute of Cost Accountants.
What is Costing ?
The technique and practice of recognising input costs at each stage of manufacturing is referred to as 'costing.' The firm uses many procedures or methods in costing, which include basic concepts and a set of rules that must be followed in order to regulate the entire process and calculate the cost of a product or service.
Cost Accounting
Cost accounting is a type of managerial accounting that tries to capture a company's overall production cost by monitoring both variable and fixed costs, such as a leasing charge. Cost accounting is used by a company's internal management department to define both variable and fixed expenses connected with the manufacturing process.
Cost accounting includes several forms of costs like Fixed costs, Operating costs, Direct costs, Variable costs, Indirect costs
Different Techniques of Costing
Marginal Costing - The premise of marginal costing is to divide all costs into fixed and variable costs.Fixed costs are unrelated to production levels. As the name implies, these costs stay constant regardless of manufacturing volume.Variable expenses fluctuate according to production levels. They are proportionate in every way. The variable cost per unit, on the other hand, remains constant.In marginal costing, we solely take these variable expenses into account when determining production costs.
Standard Costing - Standard costing is a process in which a company compares the expenses incurred for the manufacture of goods to the expenditures that should have been incurred.In essence, it is a comparison of actual costs vs conventional expenses. Variances are the discrepancies between the two.
Historical Costing - Historical costing is the process of determining and recording costs after they have occurred. It serves as a record of what has occurred and, as a result, is a postmortem of the actual costs.
Direct Costing - All direct expenses are charged to operations, processes, or products, whereas all indirect costs are written off against profits in the period in which they occur.
Absorption Costing - There is no distinction between fixed and variable costs in absorption costing. In addition, all costs, whether fixed or variable, are taken into account when calculating the cost of production. Full costing is another name for absorption costing.
Uniform Accounting - Uniform costing, unlike marginal costing, is not a different approach to cost accounting. It is one of the most recent costing and cost control approaches. It refers to all or many units in the same industry accepting and adhering to the same costing concepts and methods by mutual agreement.
FAQs on Costing Techniques: Explained
1. What are the main techniques of costing used in business?
The primary techniques of costing are used to ascertain and control costs. The main techniques include:
- Marginal Costing: Differentiates between fixed and variable costs, considering only variable costs as part of the product cost.
- Standard Costing: Compares actual costs with pre-determined standard costs to measure performance and control costs through variance analysis.
- Historical Costing: Ascertains costs after they have been incurred. It is based on recorded actual expenditure.
- Absorption Costing: Also known as full costing, it allocates all manufacturing costs, including both fixed and variable, to the products.
- Direct Costing: Charges all direct costs to operations or products while writing off indirect costs against profit in the period they arise.
- Uniform Costing: The use of the same costing principles and practices by multiple units in the same industry to ensure consistency and comparability.
2. What is the key difference between a costing method and a costing technique?
A costing method refers to the system used to determine the cost of a product or service based on the nature of the industry and production. Examples include Job Costing, Process Costing, and Contract Costing. A costing technique, on the other hand, is the principle or procedure used to analyse and present this cost information for managerial decision-making, such as Marginal Costing or Standard Costing. Methods are for cost ascertainment; techniques are for cost analysis and control.
3. How does marginal costing fundamentally differ from absorption costing?
The fundamental difference lies in the treatment of fixed manufacturing costs. In absorption costing, fixed manufacturing costs are treated as a product cost and are included in the inventory valuation. In marginal costing, fixed manufacturing costs are treated as a period cost and are written off against the profit and loss account in the period they are incurred. This distinction significantly impacts profit reporting and inventory valuation.
4. Can you provide real-world examples of how different costing methods are applied?
Yes, the choice of costing method depends entirely on the industry and the nature of its products or services. For example:
- Job Costing is used by businesses that produce unique, custom orders, such as an advertising agency, a custom furniture maker, or an architecture firm.
- Process Costing is applied in industries with continuous mass production of homogeneous products, like chemical manufacturing, oil refining, or food processing.
- Contract Costing is a variant of job costing used for large-scale, long-duration projects, such as in construction companies or civil engineering firms.
- Operating Costing is used by service industries to determine the cost of providing a service, such as transport companies (cost per passenger-km) or hospitals (cost per bed-day).
5. Why is selecting the appropriate costing technique crucial for a business's success?
Selecting the appropriate costing technique is crucial because it directly impacts pricing decisions, profitability analysis, and cost control. An unsuitable technique can lead to distorted product costs, resulting in overpricing or underpricing, which affects competitiveness. A well-matched technique provides management with accurate data for strategic decisions, such as make-or-buy choices, performance evaluation, and budgeting, ultimately guiding the company towards sustainable profitability.
6. How does the nature of a business influence its choice between job costing and process costing?
The choice is dictated by the production flow. A business producing unique, non-standardised products where costs can be traced to a specific order (e.g., a print shop making custom wedding invitations) will use job costing. Conversely, a business involved in the mass production of identical units in a continuous flow (e.g., a factory manufacturing soap) will use process costing, where costs are averaged over all units produced in a period.
7. Beyond just calculating costs, how does standard costing aid in managerial control?
Standard costing serves as a powerful tool for managerial control by establishing benchmarks. It involves setting a 'standard cost' for production. Management then compares this to the 'actual cost'. The difference, known as variance, highlights inefficiencies. By analysing variances (e.g., material price variance, labour efficiency variance), managers can pinpoint problems in the production process, take corrective action, and evaluate the performance of different departments, thereby enforcing cost discipline.
8. What is the fundamental difference between the terms 'cost' and 'price' in commerce?
The fundamental difference is perspective. Cost is the total expenditure incurred by a producer or manufacturer to create a product or service. It includes materials, labour, and overheads. Price is the monetary value that a customer pays to purchase that product or service. Essentially, cost is an internal measure for the business, while price is the external market value. Price is typically calculated as Cost + Profit Margin.
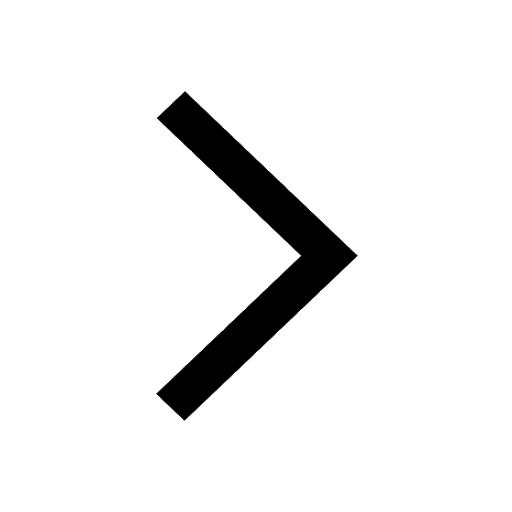
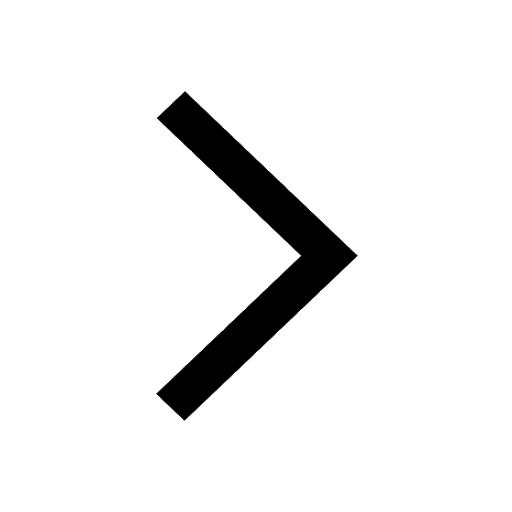
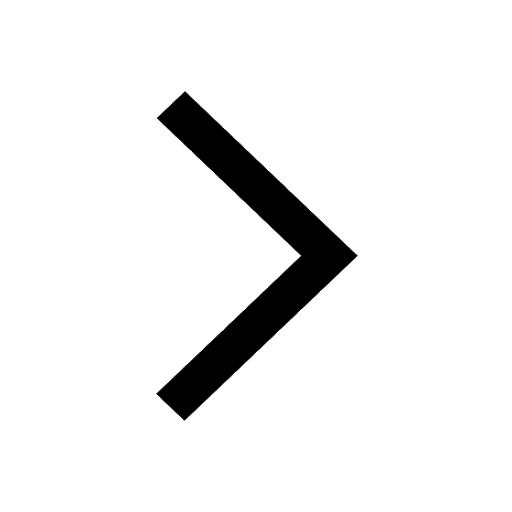
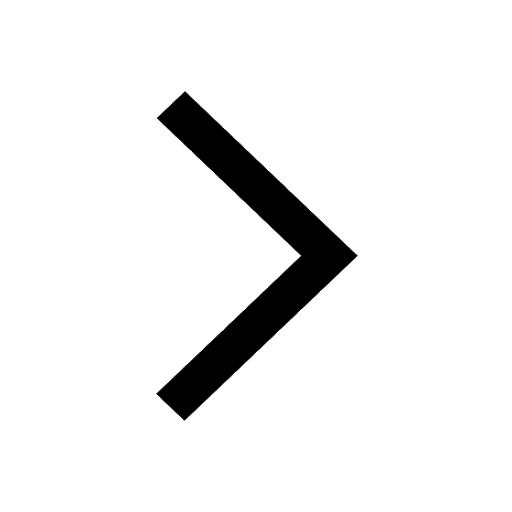
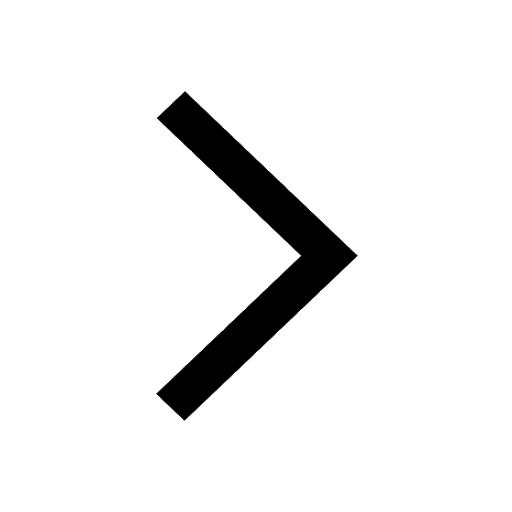
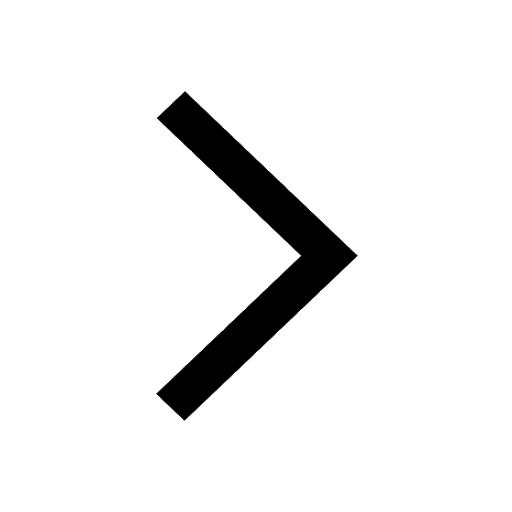
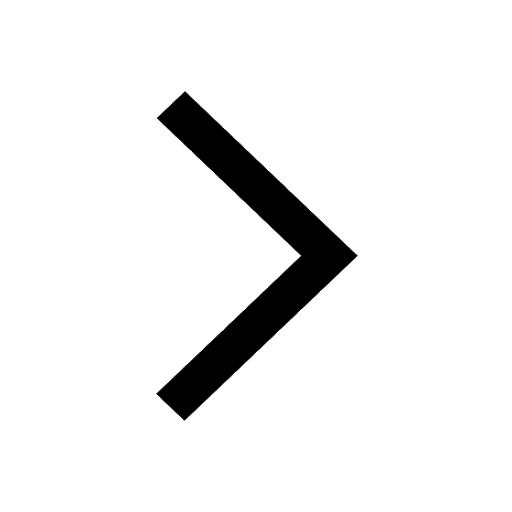
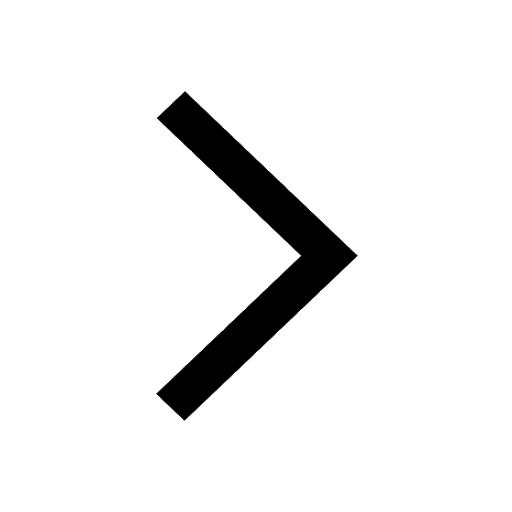
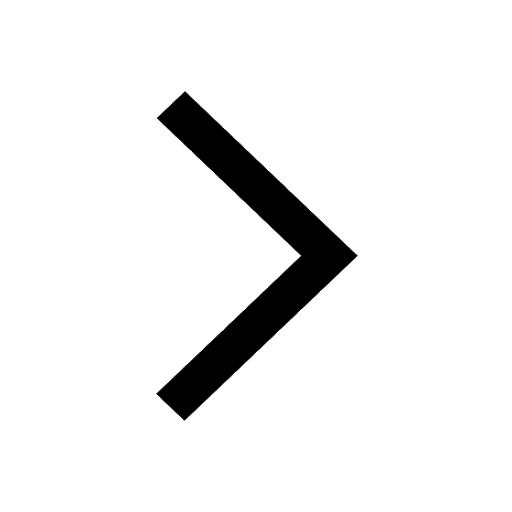
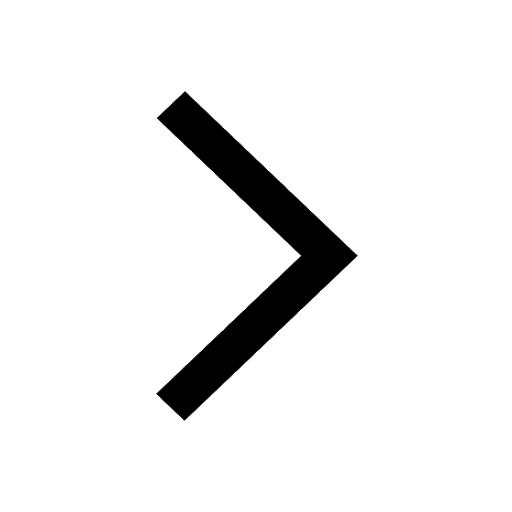
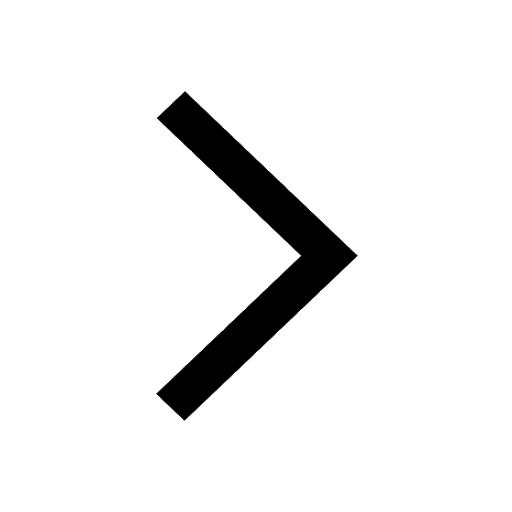
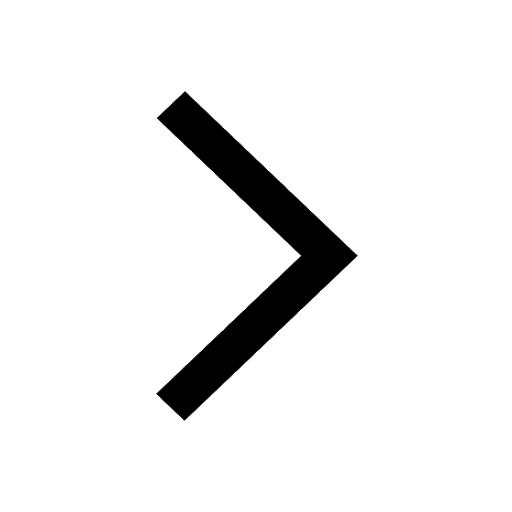