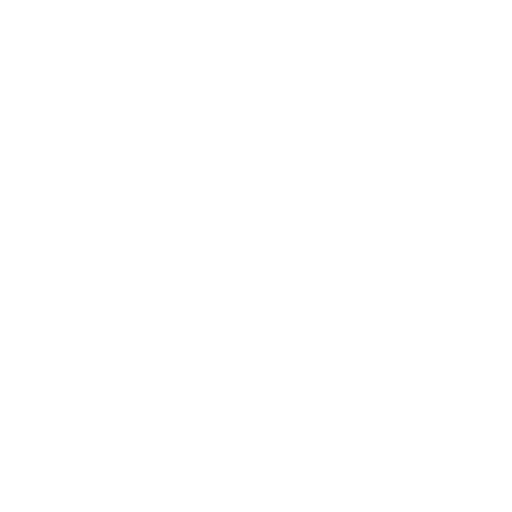

What is the Process?
By its general term, process means a series of actions or steps that is taken in order to achieve a particular end or goal. For example, filling out an expense report, checking into a hospital or filling a prescription. Whenever we execute such actions, there is always a strong motive at the back of our head i.e., to generate an output, be it a product or service, and in the process, we also most importantly generate data. This data is beneficial to control and improve the process as it works on four dimensions: quality, quantity, timeliness and cost. It would not be wrong to say that control charts are the heart of statistical process control (SPC).
What is a Control Chart?
Control charts are also known as Shewhart charts, named after Walter A. Shewhart. It is a statistical process controlling tool which helps to monitor the improvements in the process over time. For example, hospital management decides to reduce the time taken to admit someone to the hospital and thus use a solving methodology. They start by developing the process flow diagram on how people are admitted to the hospital. Next, they measure the average time taken to admit a patient each day. And finally, plot the process variables on a control chart over time.
The objective of this control chart would be to find any "special" causes of variation as well as to reflect the process improvements that have been made. Again, to effectively use control charts, understanding the information in variation is a must.
It will be more appropriate to say that the control charts are the graphical device for Statistical Process Monitoring (SPM). Control charts perpetually monitor quality depending on the number of process characteristics to be monitored. A control chart always includes a limit such as the central line for the average, an upper line for the upper control limit, and a lower line for the lower control limit. On comparing the current data to these lines, we can draw conclusions regarding whether the process variation is in control or out of control. A control chart provides us with a picture of the process variable over time and lets us know the type of variation we are dealing with as we move forward with continuous improvement. This understanding of variation is the key to using control charts effectively.
Types of Control Charts
Since now that we fully understand what a control chart means, we shall jump directly into its types.
There are Two Types of Control Charts:
1) Univariate Control Chart: As we all know ‘uni’ means one, thus a, is a graphical display (chart) of one quality characteristic is called univariate control chart.
2) Multivariate Control Chart: It is also a graphical display of a statistic that summarizes or represents more than one quality characteristic.
When to Use a Control Chart?
A control chart can be helpful to control any ongoing processes. It finds and corrects the problem as they appear.
A control chart plays an outstanding role in predicting the expected range of outcomes from a process.
It also helps in determining whether a process is in statistical control.
Control charts help to analyze the pattern of process variation from either special causes or common causes.
Lastly, it is of great help in determining whether the quality improvement project should target to prevent specific issues or to make fundamental changes to the process.
What are the Basic Procedures?
The basic procedures can be explained in the following steps:
Step 1: An appropriate control chart for the data is to be selected.
Step 2: For the collection and plotting of data an appropriate time period is to be determined.
Step 3: In this step, collection and analysis of data and construction of the chart is to be done.
Step 4: “Out of control signals” on the control chart is to be kept in mind and once it is identified, it needs to be marked on the chart and further investigation of the cause is needed.
Step 5: Keep an account of the things learnt, the cause and how it was corrected.
Step 6: The data generated needs to be plotted and with every new data, a check for new out-of-control signals.
Step 7: In case you start a new control chart and the process may be out of control, the first 20 points calculated from the control limits will be the conditional limits. You will have to recalculate the control limits if you get at least 20 sequential points from a period when the process is operating in control.
Benefits of Process Control Charts
Control charts are used by Organizations for continuous quality improvement in the following ways:
Control charts provide a simple and common language for dealing with process performance and behavior.
It aware us with decisions about which processes to leave alone and which to subject to an improvement cycle
It Limits the need for inspection.
Control charts help to determine process capability based on past performance and trends.
It can also predict future performance if the system is stable and in control.
Control charts also assess the impact of process changes.
It visualizes the performance of the process over time.
It creates a baseline for future improvements.
Communicating the performance of a process is also influenced by control charts.
FAQs on Control Charts
1. What is a Control Chart and why is it important for quality management?
A Control Chart is a statistical graph used to monitor a process over time and determine if it is in a state of 'statistical control'. Its primary importance lies in its ability to help distinguish between two types of process variation: common cause variation (natural, inherent fluctuations) and special cause variation (unexpected, assignable issues). By identifying special causes, businesses can fix problems and improve process consistency.
2. What are the three main lines on a Control Chart and what do they represent?
Every control chart has three fundamental horizontal lines that serve as reference points for the data:
- Center Line (CL): This represents the average or mean of the process data. It is the central value around which the process is expected to operate when in control.
- Upper Control Limit (UCL): This is typically set at three standard deviations above the Center Line. A data point above the UCL indicates a statistically significant positive shift in the process.
- Lower Control Limit (LCL): This is set at three standard deviations below the Center Line. A data point below the LCL suggests a statistically significant negative shift.
3. What are the main types of Control Charts used in statistics?
Control charts are broadly divided into two categories based on the type of data they monitor:
- Variable Charts: These are used for measurable, continuous data like length, weight, or time. Common examples include the X-bar chart (monitors the process average) and the R-chart (monitors process variation or range).
- Attribute Charts: These are used for discrete, countable data, often related to defects or non-conformities. Common examples include the p-chart (monitors the proportion of defective items) and the c-chart (monitors the number of defects per unit).
4. How can you tell if a process is 'out of control' just by looking at a Control Chart?
A process is considered 'out of control' when the data points on the chart display non-random patterns, signalling the presence of a special cause variation. Key indicators include:
- One or more points falling outside the Upper or Lower Control Limits (UCL/LCL).
- A run of seven or more consecutive points all lying on one side of the Center Line.
- A clear upward or downward trend in consecutive data points.
- Any obvious cyclical or repetitive pattern in the data.
5. What is the difference between common cause variation and special cause variation?
The key difference lies in their origin and predictability. Common cause variation is the natural, random 'noise' within a stable process. It is inherent and expected. For example, minor differences in a machine's output each hour. In contrast, special cause variation is due to specific, identifiable events that are not part of the normal process, such as a machine malfunction, an untrained operator, or a bad batch of raw material. Control charts are designed to detect these special causes so they can be eliminated.
6. Can a process be 'in control' but still produce poor-quality products?
Yes, absolutely. A process being 'in control' simply means it is stable and predictable. It does not necessarily mean it meets customer requirements or specification limits. For instance, a machine might consistently produce screws that are 1mm too short. The process is stable (in control), but the output is consistently defective. This highlights the difference between process control (stability) and process capability (ability to meet specifications).
7. What are some real-world examples of where Control Charts are used?
Control charts are versatile tools used across various industries. For example:
- In manufacturing, to monitor the diameter of a part, the weight of a packaged good, or the number of paint defects on a car.
- In healthcare, to track patient waiting times, the number of medication errors, or the turnaround time for lab results.
- In finance, to monitor the time taken to process a loan application or the number of data entry errors per day.
- In customer service, to track the average call handling time or the number of dropped calls per hour.
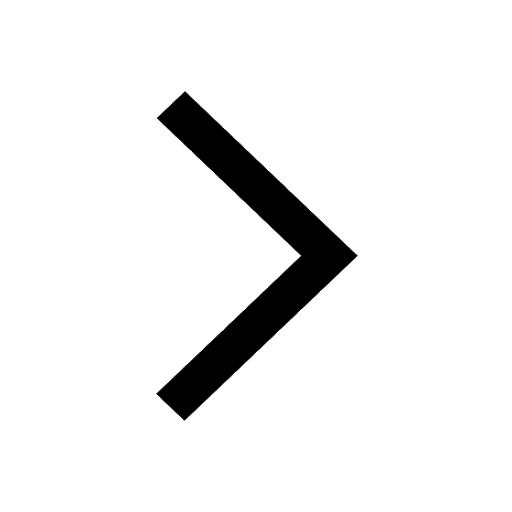
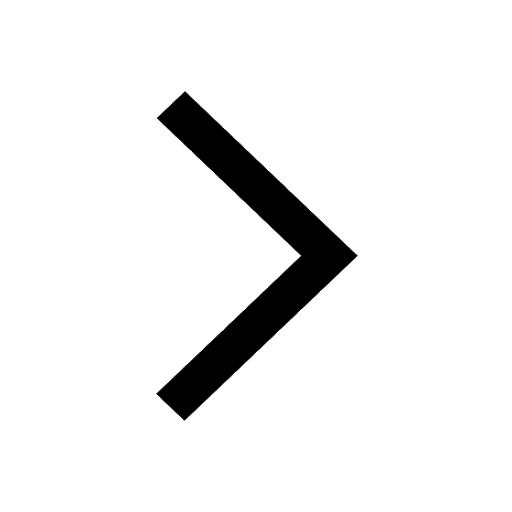
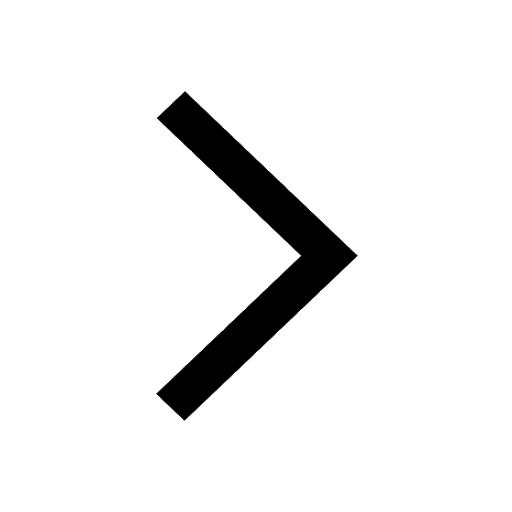
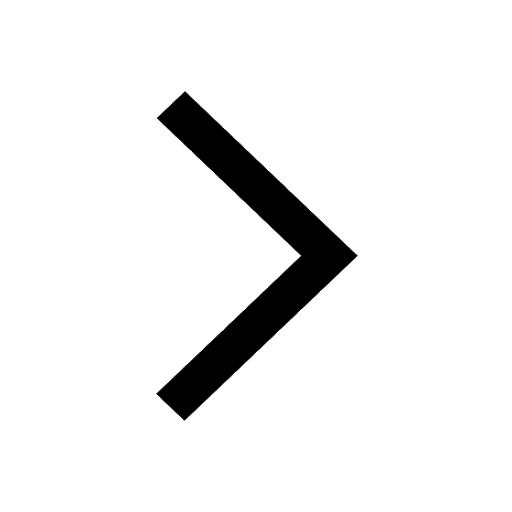
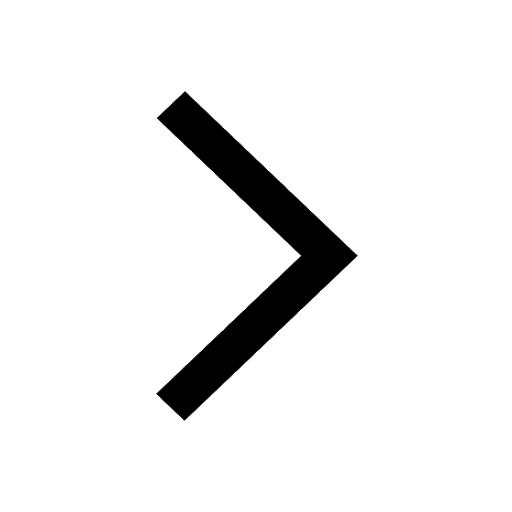
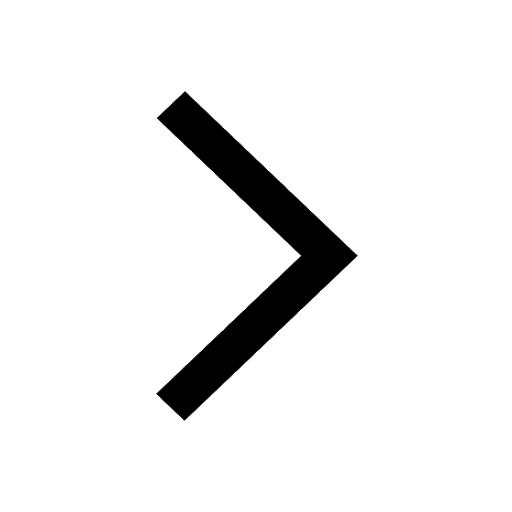
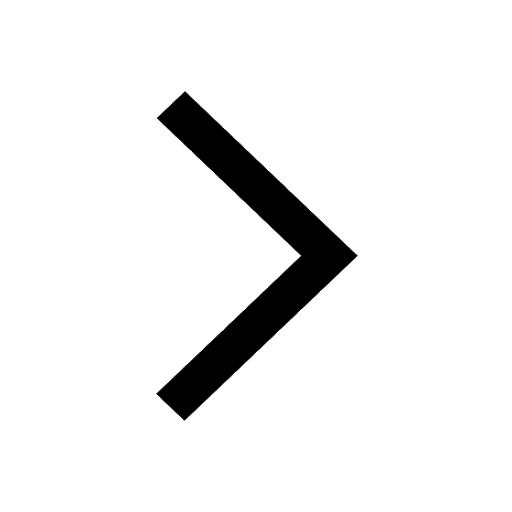
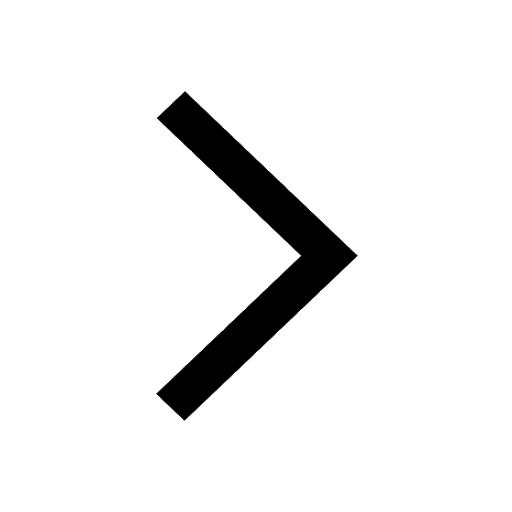
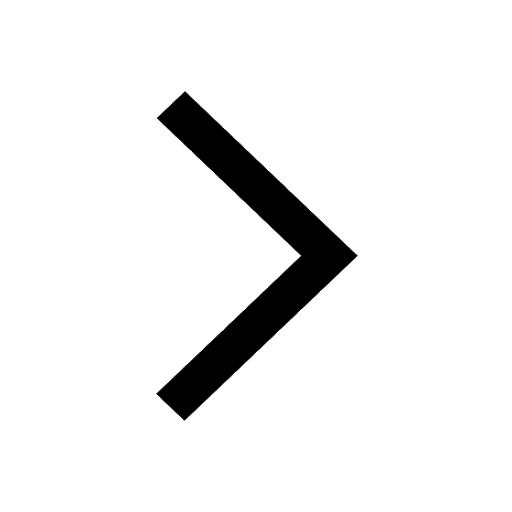
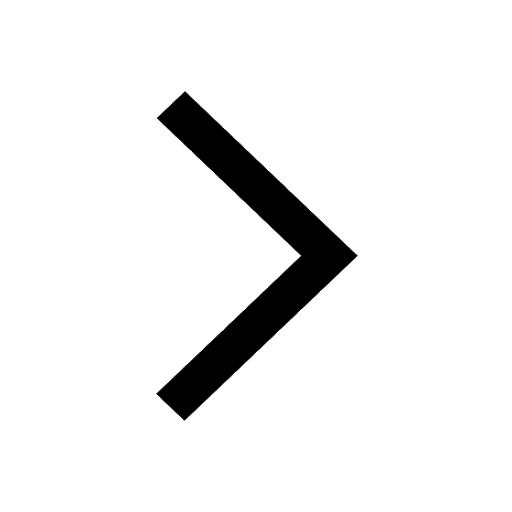
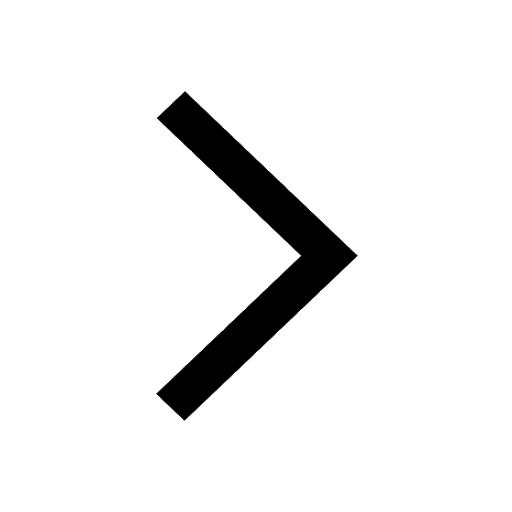
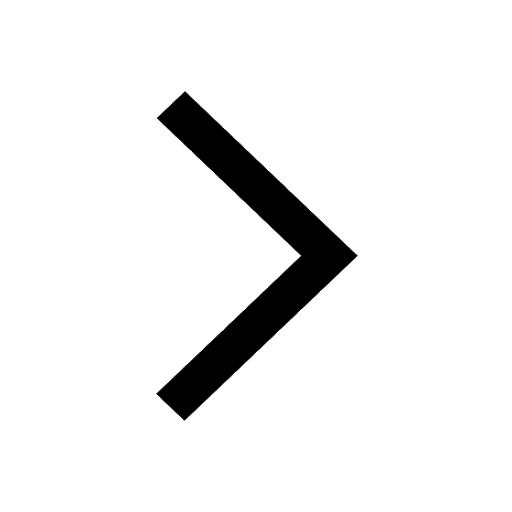
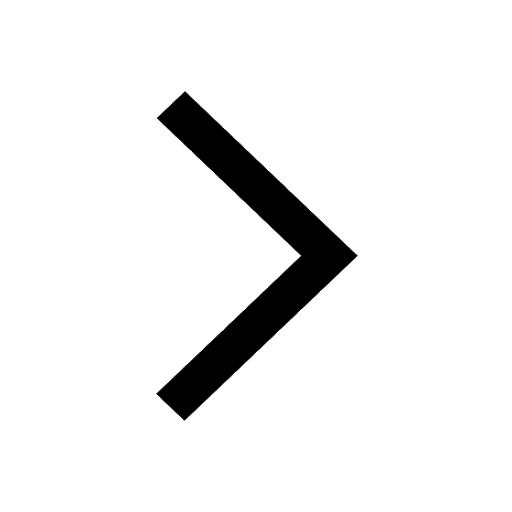
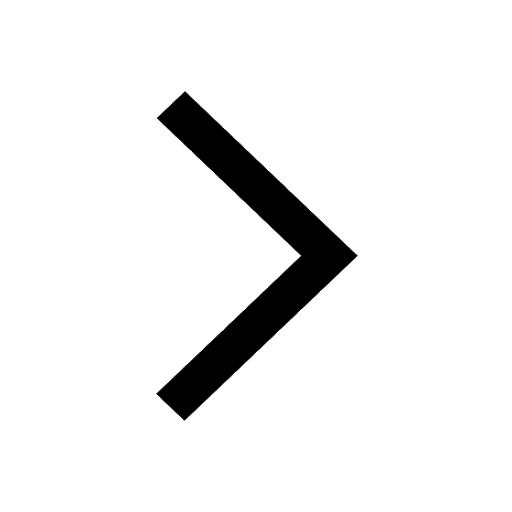
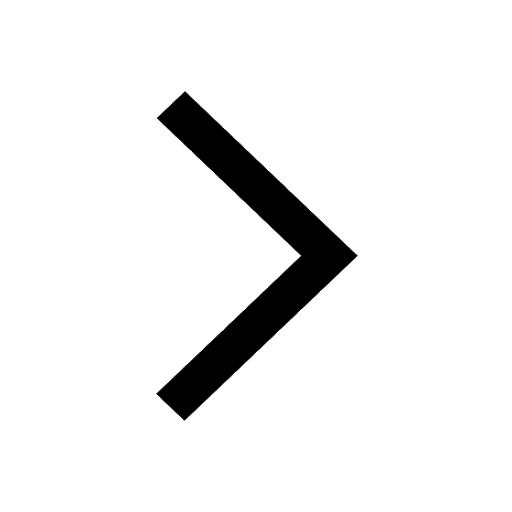
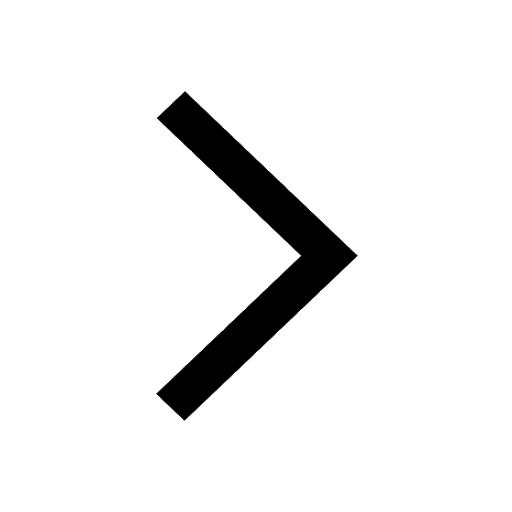
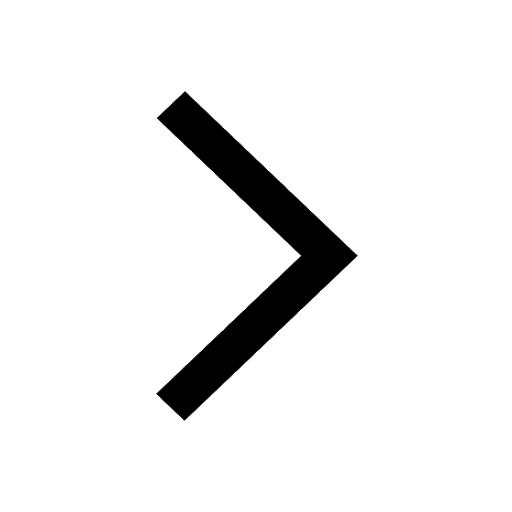
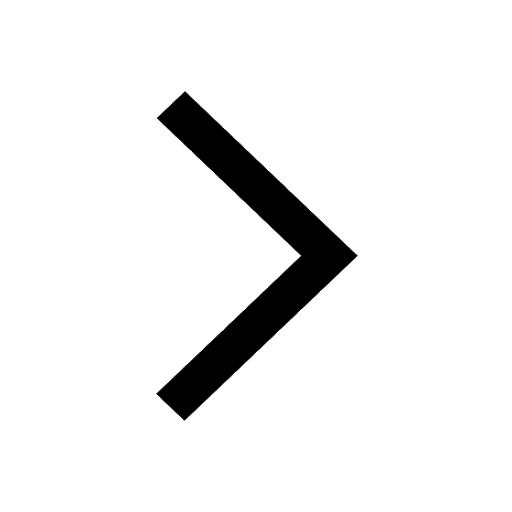