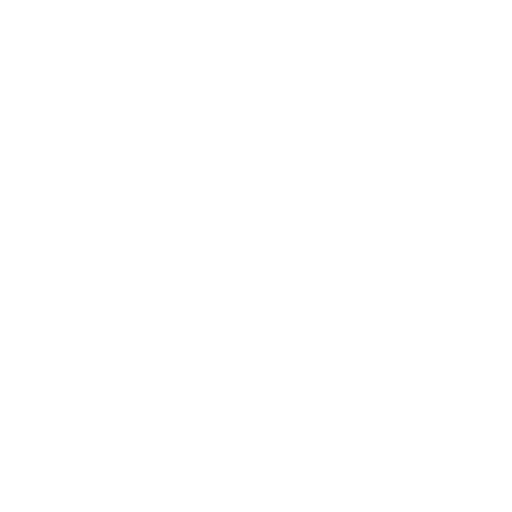

The Four Main Principles of Scientific Management by Frederick Taylor
The principles of scientific management are foundational concepts ideal for students of Business Studies, Commerce, and anyone preparing for competitive exams. Understanding these principles is essential for better exam performance and for applying scientific approaches to solve management and workplace problems in daily business life.
Principle | Description | Example |
---|---|---|
Science, Not Rule of Thumb | Replace traditional methods with scientific analysis for every job. | Timing completed using stopwatch to find most efficient way of working. |
Scientific Selection & Training | Select workers scientifically and train them for their roles. | Recruit employees using skill tests and provide job-specific training. |
Harmony, Not Discord | Ensure harmony and cooperation between management and workers. | Develop transparent communication and conflict resolution policies. |
Cooperation, Not Individualism | Promote teamwork and shared goals over competition among employees. | Group incentives rather than individual bonuses to encourage teamwork. |
Division of Work & Responsibility | Clearly divide tasks and authority between management and workers. | Managers plan; workers execute as per standardized processes. |
Principles of Scientific Management
The principles of scientific management were introduced by Frederick Winslow Taylor, known as the Father of Scientific Management. These principles are key to increasing workplace productivity and efficiency. Taylor stressed replacing traditional, experience-based practices with systematic and scientific techniques to optimize business operations.
Main Principles of Scientific Management by Taylor
Scientific management principles guide both managers and employees to improve output and streamline workflow. Taylor's four main principles are often referenced in school exams and competitive tests. Applying these principles helps organizations achieve higher efficiency.
- Replace rule of thumb methods with scientific study for all tasks.
- Scientifically select, train, and develop each worker for the job.
- Encourage cooperation between management and workers, not conflict.
- Divide work and responsibility equally between managers and workers.
Explanation of Taylor's Scientific Management Principles
1. Science, Not Rule of Thumb
This principle means that instead of relying on old habits or personal judgment (“rule of thumb”), every job should be studied scientifically. The best way to perform each task must be found using careful observation, measurement, and analysis.
2. Scientific Selection and Training of Workers
Workers should be selected based on clear criteria, and trained to fulfill specific requirements. Proper selection and consistent training lead to improved skills, higher production, and greater job satisfaction.
3. Harmony, Not Discord
Taylor believed there should be complete harmony between management and workers. Both sides must understand each other’s roles and work with mutual respect for the organization’s success.
4. Cooperation, Not Individualism
Scientific management emphasizes cooperation. Managers and employees must work as a team towards shared organizational goals, rather than competing with one another.
5. Equal Division of Work and Responsibility
Both management and employees should be equally responsible for planning and performing work. Managers should craft plans and provide support, while workers should follow instructions precisely.
Examples and Application of Scientific Management
The principles of scientific management are widely used in factories and service industries. For example, in an automobile plant, time and motion studies help optimize how workers assemble parts. In a restaurant, standardizing steps for preparing a dish reduces errors and improves customer service. By applying Taylor's techniques, businesses increase productivity and reduce waste.
- Using a stopwatch to find the quickest, best way to pack boxes (Science, Not Rule of Thumb).
- Selecting employees with proper skills and providing them training (Scientific Selection).
- Conducting regular team meetings to ensure smooth operations (Harmony and Cooperation).
- Assigning clear duties to managers (planning) and workers (doing the work) (Division of Work).
Difference Between Taylor and Fayol’s Principles of Management
Basis | Taylor’s Principles | Fayol’s Principles |
---|---|---|
Focus | Shop-floor level, improving efficiency and work methods | Top-level, overall management of organization |
Approach | Scientific analysis of tasks and workers | Administrative functions and processes |
Number of Principles | 4 major, several minor | 14 |
Known For | Functional foremanship, mental revolution, time and motion studies | Unity of command, discipline, scalar chain |
Explore more at Difference Between Fayol and Taylor's Theories of Management.
Techniques and Impact of Scientific Management
Taylor introduced techniques like time and motion study, functional foremanship, and the differential piece-rate system. These methods helped in developing best practices, fair wages, and optimal use of resources. Scientific management shaped modern industries and is still relevant in ensuring task efficiency and productivity today.
- Time and Motion Study: Measuring time for each small task to eliminate waste.
- Differential Piece-Rate System: Paying higher rates for higher output.
- Functional Foremanship: Dividing managerial work among several specialists for better supervision.
Read about more techniques at Techniques of Scientific Management.
Use Cases for Students and Business
Knowledge of scientific management helps students answer exam questions, tackle case studies, and apply principles in group projects. For business professionals, using these concepts leads to improved workplace organization and profitability. At Vedantu, we simplify Commerce topics like scientific management for exam success and practical understanding.
Related reading: Taylor Principles of Management, Features and Importance of Controlling, and Organizing.
Summary
The principles of scientific management, founded by Frederick Taylor, focus on replacing old habits with scientific study, team cooperation, and clear division of work. These concepts are crucial for students and professionals, boosting both academic performance and business efficiency. Applying Taylor’s ideas ensures systematic, productive workplaces and better exam results.
FAQs on Principles of Scientific Management: Key Concepts and Examples
1. What are the four core principles of scientific management as given by F.W. Taylor?
Frederick Winslow Taylor, the Father of Scientific Management, introduced four fundamental principles to enhance workplace efficiency. As per the CBSE Class 12 syllabus for 2025-26, these are:
- Science, Not Rule of Thumb: Replacing old, intuitive work methods with scientifically proven, optimal techniques.
- Harmony, Not Discord: Fostering complete understanding and positive relations between management and workers to prevent conflict.
- Cooperation, Not Individualism: Promoting teamwork and mutual cooperation over internal competition to achieve organisational goals.
- Development of Each and Every Person to His/Her Greatest Efficiency and Prosperity: Scientifically selecting, training, and developing employees to maximise their potential.
2. What is the importance of 'Science, Not Rule of Thumb' in management?
The principle of 'Science, Not Rule of Thumb' is crucial because it replaces guesswork and traditional methods with a systematic, data-driven approach. It involves scientifically analysing each element of a job to determine the one best way to perform it. This leads to increased efficiency, reduced wastage of time and resources, and standardised processes, which are essential for large-scale production.
3. What are some key techniques of Scientific Management?
Beyond the core principles, F.W. Taylor developed several techniques to apply scientific management on the shop floor. Key examples include:
- Functional Foremanship: Dividing supervisory roles into specialised functions to improve oversight.
- Time and Motion Study: Analysing the time and movements required for a task to eliminate inefficiencies.
- Differential Piece-Rate System: A wage system that pays workers based on their output, rewarding high-performers with higher rates.
- Standardisation and Simplification of Work: Setting standards for every business activity and eliminating unnecessary variations in products.
4. How do Taylor's and Fayol's management principles differ?
The primary difference lies in their focus. Taylor's Scientific Management concentrates on improving productivity at the shop-floor or operational level, focusing on worker efficiency. In contrast, Fayol's Administrative Principles provide guidelines for top-level managers on how to run the entire organisation. Taylor's approach is a micro-level perspective, while Fayol's is a macro-level perspective.
5. What is the main objective of the 'Harmony, Not Discord' principle?
The main objective of 'Harmony, Not Discord' is to achieve a complete mental revolution on the part of both management and workers. It aims to transform their thinking so they see each other as partners, not adversaries. Taylor believed that organisational prosperity depends on mutual trust and understanding, ensuring that gains are shared and conflicts are resolved collaboratively for the benefit of all.
6. Are Taylor's principles still relevant in modern, digital-era businesses?
Yes, the core logic of Taylor's principles remains highly relevant today. While the context has shifted from factory floors to digital workflows, the emphasis on optimisation, efficiency, and data-driven decision-making is fundamental to modern business practices. Concepts like A/B testing in marketing, process automation (RPA), and workflow analysis in software development are modern applications of the scientific approach to work.
7. What are the main criticisms of Scientific Management?
The main criticisms of Scientific Management often centre on its potential to dehumanise the workforce. Critics argue that it can lead to monotony by over-specialising tasks, stifle worker creativity and initiative, and place excessive emphasis on productivity at the expense of employee well-being and job satisfaction. It is sometimes seen as overly mechanistic and unsuitable for creative or knowledge-based work.
8. How can scientific management be applied in a service industry like a fast-food restaurant?
In a fast-food restaurant, scientific management principles are widely used to ensure consistency and speed. For example:
- Time and motion studies are used to design the kitchen layout and standardise the exact steps for preparing a burger or fries.
- Scientific selection and training ensure every employee follows the same procedure, guaranteeing product quality.
- Standardisation of work means customers receive the same product regardless of who prepares it, improving customer service and efficiency.
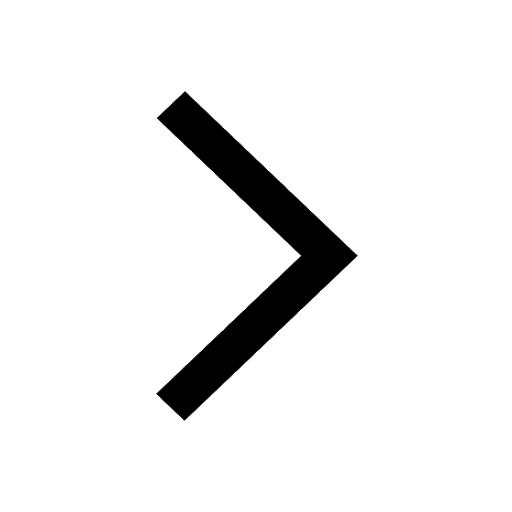
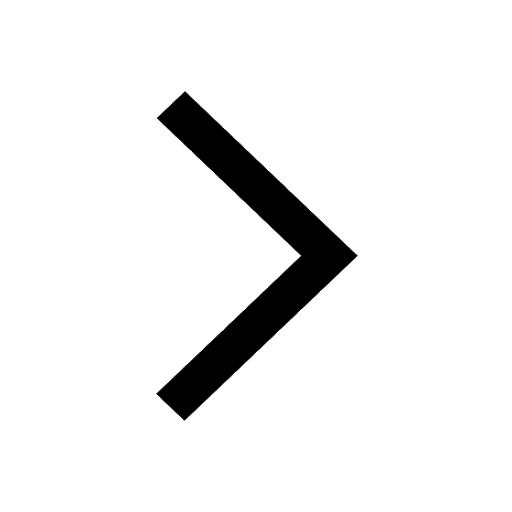
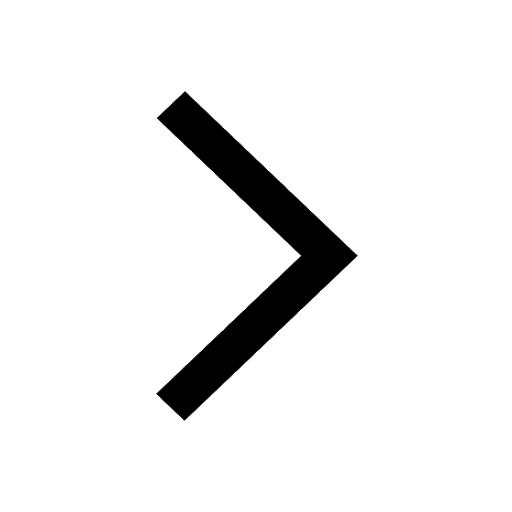
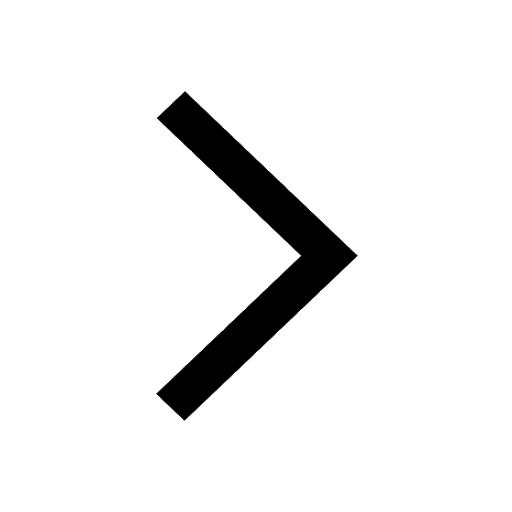
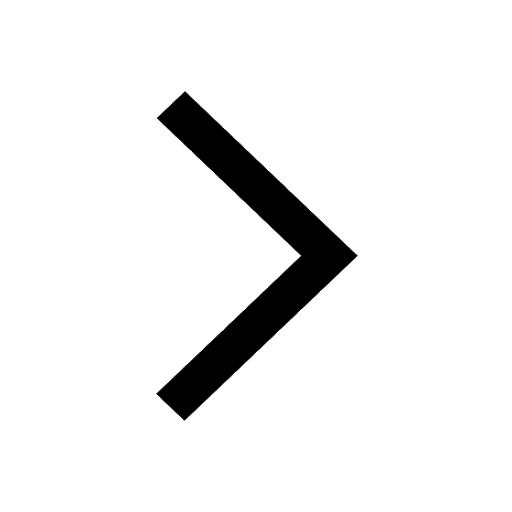
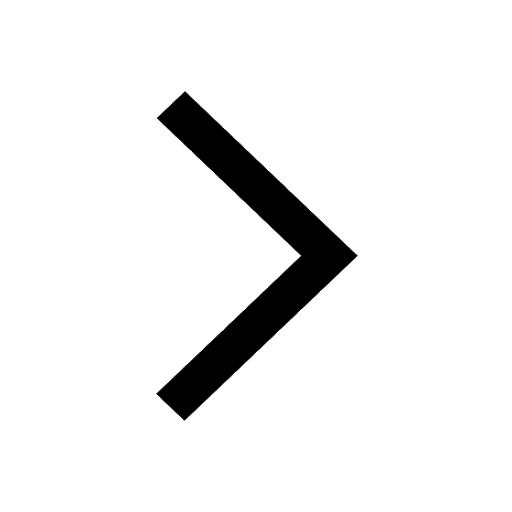
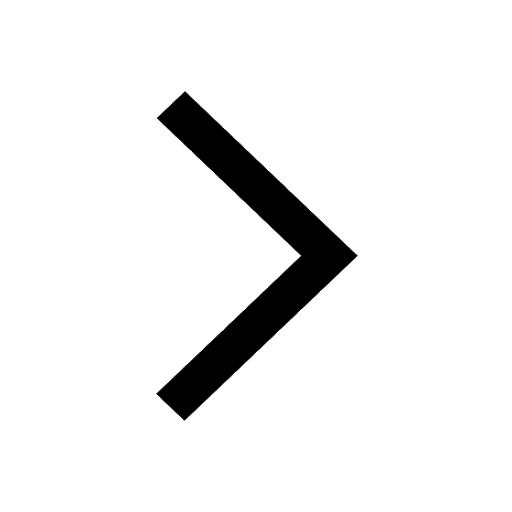
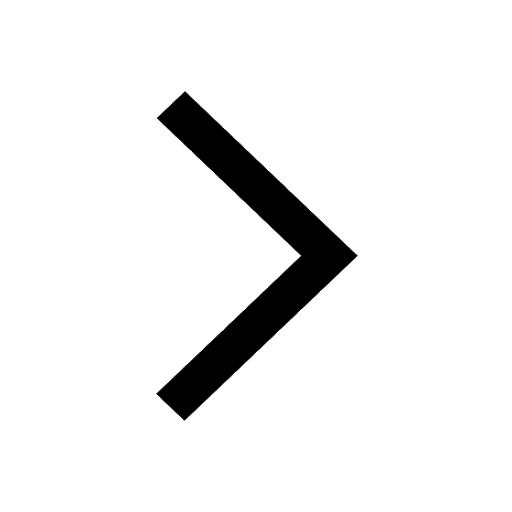
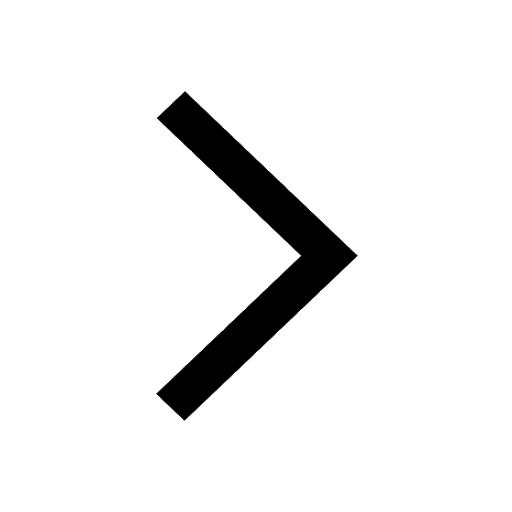
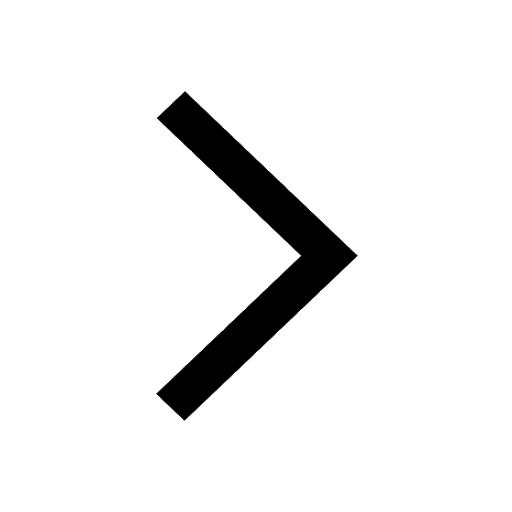
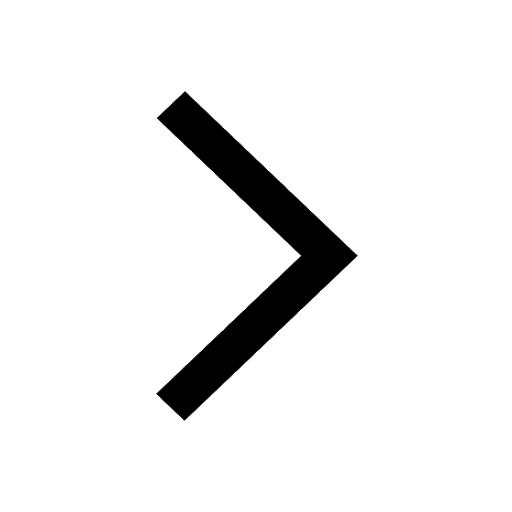
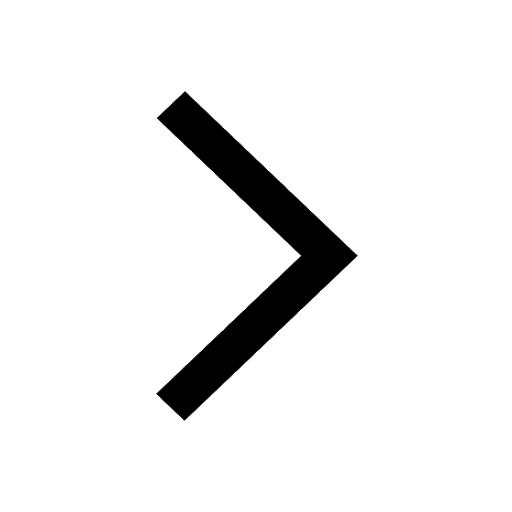
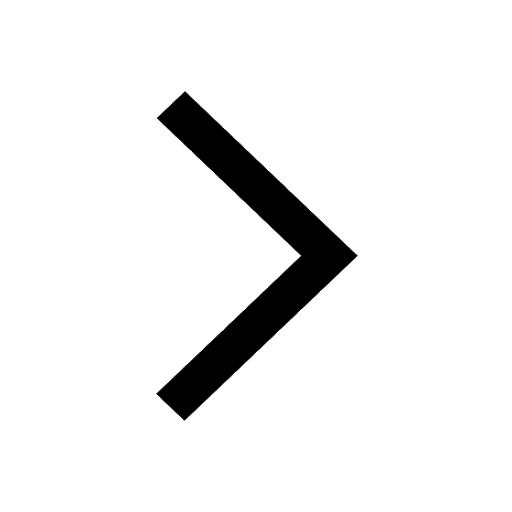
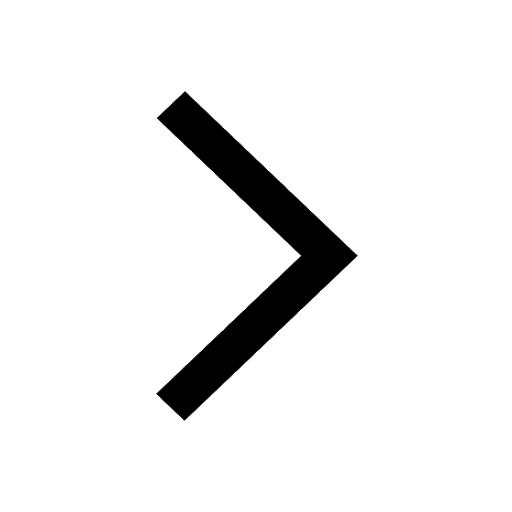
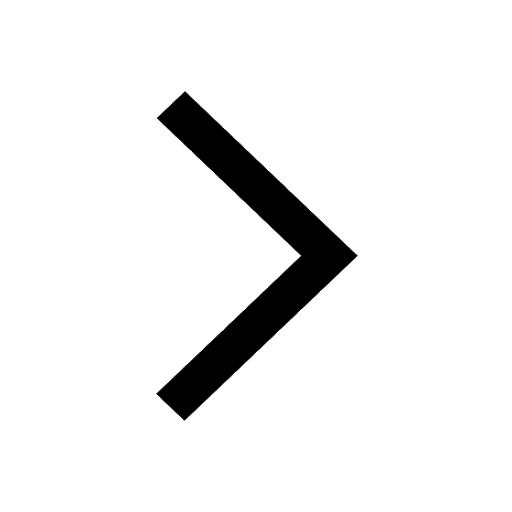
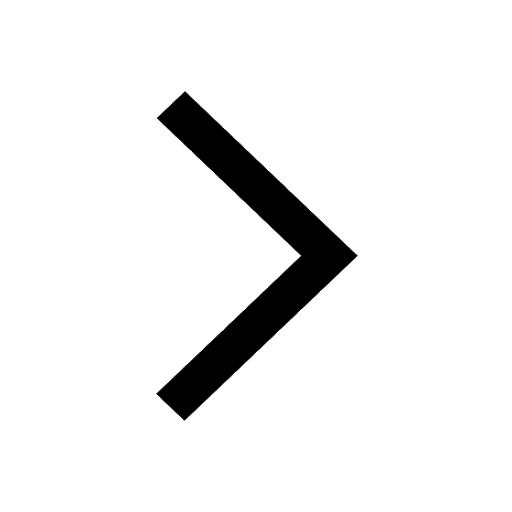
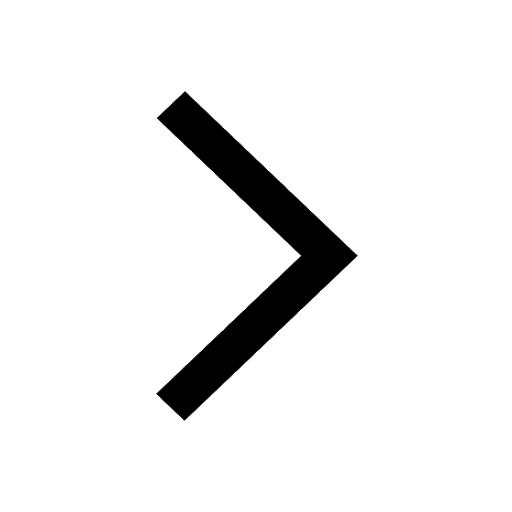
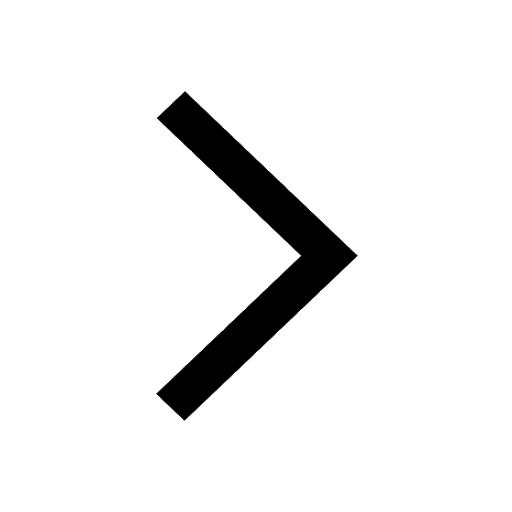